In this article, you will learn how to design a steel beam. In the previous article, we discussed the different types of sections used as steel beams. We have also discussed the different properties which are important as a steel beam.
The steps for the design of the steel beam depend upon whether the beam is laterally supported or laterally unsupported. In this section, we will learn how to decide whether the section has lateral support or not and what are the design steps.
Section classification of steel beam
As in the previous section we have discussed that the design steps depend on whether the section is laterally stable or unstable. Hence in this section, we will learn how to classify the section. Apart from this, the section classification is also very important.
The IS-800 : 2007 divided the section is four categories which are as follows:
- Slender section: The sections which are very weak in torsional rigidity we keep it under slender sections. To decide whether the section is slender or not we can use Table -2 of IS 800-2007.
- Semi-compact section: It is more rigid than the slender section. To resist the load this section can take stress up to yield stress.
- Compact section: Compact section is more stable than the other two. It can go up to plastic moment capacity by can not retain it for large rotation.
- Plastic section: These sections can go up to plastic moment capacity and can hold it for large rotations.
IS – 800: 2007 decides this classification on the basis of the width-to-thickness ratio of the flanges and of the web.
How to find the laterally supported beams
In this section, we will learn how we will decide whether we have a laterally supported beam or not. If you can find the lateral restrain in the compression flange of the beam then we call it a laterally supported beam. This we can see in the figure below.
In simple words, if you find some mechanism which is not allowing the flange to do lateral movement then we have a laterally supported beam. This restricts the buckling of the compression flange of the beam.
There are different methods to provide effective restraints:
- Shear connectors
- Cross bracings
- Cross frames
- Diaphragm
Against this if we have the beam where no such mechanism is provided which can restrict the movement of the compression flange. We call this a laterally unsupported beam. In this type of beam, there is always the possibility of buckling of the compression flange.
Design strength in bending (Flexure) for laterally supported steel beams
As discussed in the code IS 800-2007 the design bending strength of the steel beams which is adequately supported against lateral torsional buckling is governed by the yield stress criteria. Section 8.2.1 of the IS- 800:2007 refers to the design of laterally supported beams and if the beams are laterally not supported we design them by using section 8.2.2.
The design moment at any section in a beam shall satisfy
$$M\le M_d$$
Where $M_d$ = Design bending strength of the section.
- When $d/t_w < 67 \varepsilon$, there is no shear buckling
- d is the depth of web
- $t_w$ is the thickness of the web
- When $d/t_w > 67 \varepsilon $, web of the beam is susceptible to shear buckling.
Design of laterally supported beams using clause 8.2.1
In this section, we will design the beams which are laterally supported. We will discuss the different clauses which give the step-by-step procedure for the design of the beam.
Clause 8.2.1.2 IS -800: 2007 for steel beams
This clause of the IS code says that the, when factored design shear force is not more that 0.6 $V_d$, where $V_d$ is the design shear strength of the cross-section. Here we will take the design bending strength $M_d$:
$$M_d = \beta_b Z_b f_y/ \gamma_{mo}$$
In this formula, we will calculate the design bending strength. And to avoid the irreversible deformation under serviceability loads $M_d$ shall be less than:
- $1.2 Z_e f_y/\gamma_{mo}$ in case of simply supported beam
- $1.5Z_e f_y/\gamma_{mo} in cantilever beams
- $\beta_b = 1.0$ for plastic and compact section
- $\beta_b = Z_e/Z_p for semi-compact sections
- $Z_p$, and $Z_e$ = plastic and elastic section moduli of the cross section
- $f_y$ = yield stress of the material and
- $\gamma_{mo}$ = partial safety factor (You can see Table 5 of Page 30)
Clause 8.2.1.3 IS- 800: 2007 for steel beams
In the previous section, the shear force was less than 0.6 $V_d$. In this section, we will discuss the design strength when the design shear force exceeds the 0.6 $V_d$. Here the $M_d$ shall be taken as:
$$M_d = M_{dv}$$
- Where $M_{dv}$ = design bending strength under high shear as defined in Clause 9.2. This clause deals with the combined shear and bending.
Combined shear and bending in steel beams
As discussed above the present section explains the determination of the design strength of the beam when subjected to heavy shear. Clause 9.2.1 of the section says that there will be no reduction in the moment capacity of the section is necessary as long as the cross-section we didn’t find the high shear force. We can take the moment capacity as $M_d$ without any reduction.
When we find the factored value of the applied shear force exceeds the limit. In this case, code suggests that the factored moment of the section must be less than the moment capacity of the section. We can calculate the reduced moment capacity of the section as explained in the following section.
Moment capacity for the sections can be calculated as follows:
- Plastic section or compact section: The reduced moment capacity for the plastic or compact section can be calculated using the following formula. $$M_{dv} =M_d-\beta(M_d-M_{fd}) \le 1.2 Z_ef_v/\gamma_{mo}$$
- Semi-compact section: For the semi-compact section the we calculate the design strength as $M_{dv} = Z_ef_y/\gamma_{mo}$.
Where $M_d$ is the plastic design moment of the while section disregarding high shear force effect (see 8.2.1.2)=$\beta_b Z_pf_v/\gamma_{mo}$.
$\beta = (\frac{2V}{V_d}-1)^2$
V= factored applied shear force as governed by web yielding or web buckling
$V_d$ = design shear strength as governed by web yielding or web buckling
$M_{fd}$ = plastic design strength of the area of the cross-section excluding the shear area, considering partial safety factor $\gamma_{mo}$.
$Z_e$ = elastic section modulus of the whole section.
Effects of holes in the tension zone
In this section we will discuss the effect of the holes in the tension zone. The clause 8.2.1.4 of the IS 800 :2007 deals with it. It says the effects of holes in the tension flange, on the design bending strength we don’t need to consider if: $$\frac{A_{nf}}{A_{gf}}\ge \frac{f_y}{f_u} \times \frac{\gamma_{m1}}{m0}\times \frac{1}{0.9}$$
Where $\frac{A_{nf}}{A_{gf}} = ratio of net to gross area of the flange in tension.
$\frac{f_y}{f_u}= ratio of yield and ultimate stress if the material
$\frac{\gamma_{m1}}{\gamma_{m0}} = ratio of partial safety factors against ultimate to yield stress.
The code says when $A_{nf}/A_{gf}$ does not satisfy the above requirement, the reduced effective flange area, $A_{ef} satisfying the above equation we may take as the effective flange area in tension.
Shear lag effects
In this section, we will see the shear lag effects in the flanges.
The IS-800 : 2007 says that the shear lag effects in flanges need not to be regarded if:
- Supported along one leg: For the out-stand elements $b_o \le L_0/20$
- Supported along two edges: For internal elements $b_i \le L_0/10$
Where $L_0$ is the length between points of zero moments (inflection) in the span, $b_O$ is the width of out-stand flange with out-stand, and $b_i$ is the width of the flange as an internal element.
Code also recommends that if we find that these limits are exceeded than we have to calculate the effective width of the flange for design strength using specialist literature.
Conclusion
In this article, we have learned how to design the beam for flexure. We only discussed the design of the laterally supported beams. In the next post, we will discuss the design of laterally unsupported beams.
We have learned the following key points in this article:
- Section classification: We have learned how to classify the section based on the width-to-thickness ratio.
- Flexure strength: We have seen how to calculate the flexural strength of steel beams according to the provisions given in the code.
- Combined effects: In this article, we have also discussed when to consider the combined shear and bending effects while calculating the strength of the beam.
- Shear lag effect: We have discussed the shear lag effects and also discussed the different conditions when to ignore the shear lag effects.
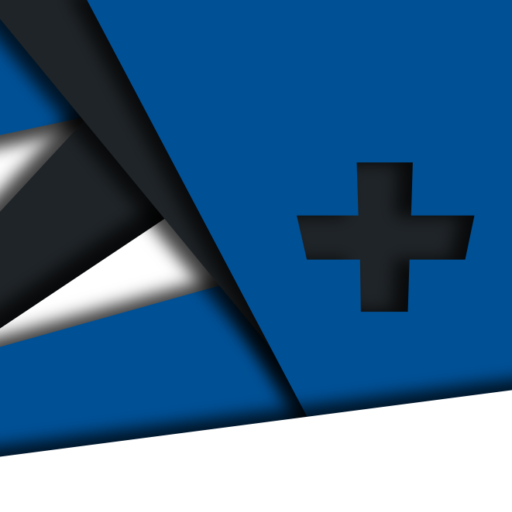
Android Apps
⭐️ ⭐️ ⭐️ ⭐️ ⭐️ 1000+ | 400,000 + Downloads (Cumulative)
At eigenplus, our goal is to teach civil engineering students about structural analysis and design starting from the fundamental principles. We do this with the help of interactive android applications and accompanying web articles and videos.
Our apps have helped more than 400 thousand students across the world to understand and learn the concepts of structural engineering. Check out our apps on the google play store.
This article was crafted by a group of experts at eigenplus to ensure it adheres to our strict quality standards. The individuals who contributed to this article are:
Author
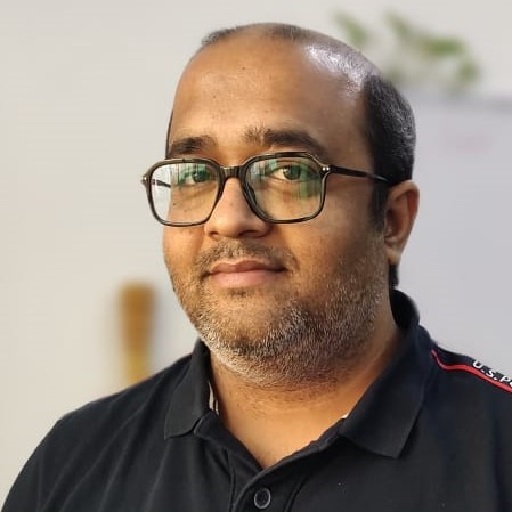