As a civil engineer, it’s always important to learn the key points needed for designing any member. The article on design strength describes easy steps to compute the compressive design strength, $P_d$ of the column as per IS 800:2007. In this article, we will see simple steps on how to design a column.
Note: You can apply this concept to the design of I-section, Channel section, and Double-angle sections columns but not to single-angle sections.
What are the basic informations needed to start the design?
To design a axially loaded compression member, the following things are required:
- Length of the member
- Boundary conditions
- Load it has to support $($also called design load, $P)$
Now a compression member should be designed such that it’s design compressive strength, $P_d$ should be greater than design factored load, $P$ i.e., $P_d>P$.
Design: an AB process → Assumption and Backing
Assumption:
It is obvious that the designer has to select a cross-section such that $P_d>P$. Now, to compute $P_d$, the key ingredient is slenderness ratio $\lambda = KL/r$. From the given information, we know the value of $KL$ which thus sums up to finding appropriate radius of gyration, $r$.
Thus, a designer has to adopt following two steps:
- Step A: Assumption → Assume $\lambda$ to find a trial cross-section for which $P_d>P$.
- Step B: Backing → Use design equations of IS 800:2007 to compute $f_{cd}$ and confirm $P_d>P$.
Let us look at some thumb rule to design a with an example for better understanding the design process.
Design Example with step-by-step procedure for design of a compression member
Design a 4.0 meters long column to carry a factored design load of 900 kN. The column is restrained in both rotation and translation. Use Fe410.
Step 1: Assume $\lambda$
As a thumb rule for columns of height 3.5 m to 5 m, a value between 40 to 60 you can assume. If the factored load is more (>1000 kN) smaller value of slenderness (~40) you have to assume. Whereas for longer lengths of columns (> 5, m), a higher value of slenderness should be assumed (60 < $\lambda$ <90).
For the given problem, as the column height is 4.0 meters and factored load is 900 kN, let us assume $KL/r=50$.
Step 2: Choose a buckling class for the member
For the given problem, determine the buckling class for the member. Using $\lambda$, $f_y$, and Table 9, IS 800:2007 to determine compressive stress, $f_{cd}$.
Tips: For I-Section, unless specified, assume member to fail minor axis buckling as $(r_y<r_x)$.
For the given problem, the cross-section type is I-section which will undergo minor axis flexural buckling as $(r_y<r_x)$. The buckling class as per Table 10, IS 800:2007 is “buckling class b” provided $h/b_f>1.2$ and $t_f<40\; mm$.
We assumed $KL/r=50$ and $f_y=250\; MPa$ and for buckling class b, $f_{cd}$ from Table 10, IS 800:2007 is $194 \; MPa$.
Remaining steps for the design a compression member
Step 3: Determine required cross-sectional area $A$
The required cross-sectional $A$ you can calculate as
$$ A=\frac{800\times 10^3}{194}=4639 \; mm^2 $$
Step 4: Choose a suitable cross-section from IS Handbook SP 6:(1)
The required area as per assumption is $4639 \; mm^2$. Choosing section ISHB 200 @ 37.3 kg/m as $A=4754 \; mm^2>4639\; mm^2$.
Step 1 to Step 4 concludes Step A: Assumption.
Now,
Step 5: Computing $f_{cd}$ for chosen section.
Follow blog to find out elaborate steps on computing $f_{cd}$.
In the current example,
For section ISHB 200 @ 37.3 kg/m;
$$ A=4754 \; mm^2\; I_{xx}=3608.4\times 10^{4} mm^4;\; I_{yy}=967.1\times 10^4 \; mm^4 $$
$$ r_{x}=87.1\;mm ; \; r_{y}=45.1 \; mm $$
You know that the column is having to restrain in rotation and translations. Hence, from Table 11, IS 800:2007,
$$ KL=0.65 \times 4000=2600\; mm $$
Now,
$$ \lambda_x=\frac{2600}{87.1}=29.85\quad \quad \lambda_y=\frac{2600}{45.1}=56.65 $$
Since, $\lambda_y<\lambda_x$, Minor axis buckling. From Table 10, IS 800:2007, buckling class is “b”.
Now, using Table 9(b) for $f_{cd}$ for $KL/r=56.65$ and $f_y=250\; MPa$; we have
$$ f_{cd}= 185.35\; MPa\;\implies P_d=A\times f_{cd}=4754\times 185.35 = 881 \; kN < 900 \; kN $$
The current section ISHB 200 @ 37.3 kg/m is not sufficient to resist the factored load of 900 kN. Thus, we have to adopt a different cross-section.
Is design always an iterative process? → No
In the current design example we chose area of cross-section just above the required cross-section. It is advisable to increase the the required area of cross-section by 20% while choosing a cross-section in order to not make the design an iterative process.
So now, lets check for ISHB 225 @ 43.1 kg. Now we have
$$ A=5494\; mm^2\\ I_{xx}=5279.5\times 10^{4} mm^4;\;I_{yy}=1353.8\times 10^4\; mm^4 $$
$$ r_{x}=98\;mm; \; r_{y}=49.6\;mm $$
Now,
$$ KL=2600\;mm \quad \therefore \lambda_x=\frac{2600}{98}=26.53\quad \quad \lambda_y=\frac{2600}{49.6}=52.42 $$
Since, $\lambda_y<\lambda_x$, Minor axis buckling. From Table 10, IS 800:2007, buckling class is “b”.
Now, using Table 9(b) for $f_{cd}$ for $KL/r=52.42$ and $f_y=250\; MPa$; we have
$$ f_{cd}= 190.85\; MPa\;\implies P_d=A\times f_{cd}=5494\times 190.85= 1049\; kN > 900 \; kN $$
Thus, adopt ISHB 225 @ 43.1 kg/m as desired cross-section to resist the factored load of 900 kN
Conclusions
While the design of compression members might be tricky, it requires just experience and practice to do the the simple process AB i.e., Assumption and Backing. In this article we covered the design example and have seen simple steps to design a compression member. In the upcoming articles, we will encounter problems where single section column will not alone be able to resist the heavier factored load.
From this article, you have learned the following key points:
- Design: You have learned the simple AB process to design a column.
- Assumptions: We have also learned how to take initial assumptions while we are designing the column.
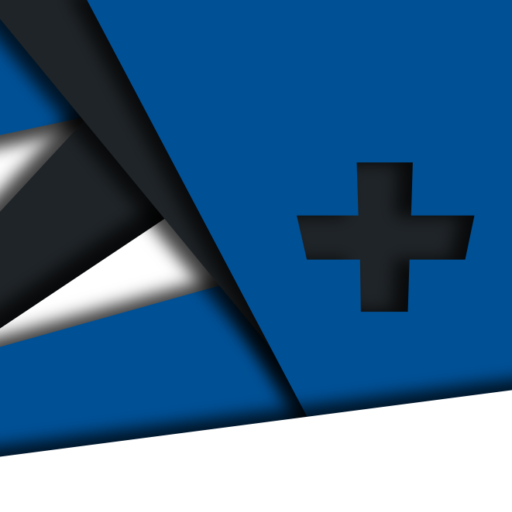
Android Apps
⭐️ ⭐️ ⭐️ ⭐️ ⭐️ 1000+ | 400,000 + Downloads (Cumulative)
At eigenplus, our goal is to teach civil engineering students about structural analysis and design starting from the fundamental principles. We do this with the help of interactive android applications and accompanying web articles and videos.
Our apps have helped more than 400 thousand students across the world to understand and learn the concepts of structural engineering. Check out our apps on the google play store.
This article was crafted by a group of experts at eigenplus to ensure it adheres to our strict quality standards. The individuals who contributed to this article are:
Author
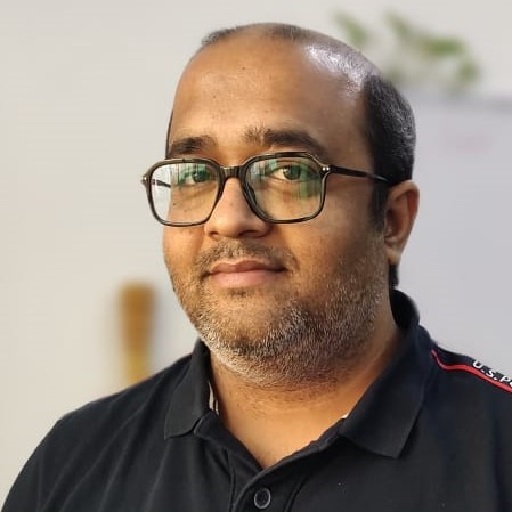