In our previous post, we explored different types of steel shapes. However, when it comes to transferring loads from one component to another, connections play a crucial role. These connections can take the form of either bolted or welded joints. Therefore, in this post, we will focus on the various types of weld connections that are commonly used in constructing steel buildings, bridges, and other structures.
Welding is a crucial process in a wide range of industries, from manufacturing and construction to automotive and aerospace. For example, in the construction industry, welding is used to join structural steel and create strong, durable buildings and bridges.
Welding is the process of joining two or more pieces of metal or thermoplastic materials. Various types of welds are used in construction, such as butt welds, fillet welds, plug welds, and many others.
Butt weld
Butt welding, a welding technique used to join two pieces of metal end-to-end, also known as groove welding, requires the metal’s edges to be prepared before the weld is created. Although groove welds are more expensive due to the necessary edge preparation, they are safe to use in heavily stressed members. However, square butt welds can only be provided up to a plate thickness of 8mm.
Nonetheless, butt welding is commonly used in the construction of pipes, tubing, bridges, and buildings. Overall, this technique is essential in various industries, and its applications depend on several factors, including material type, thickness, and load-bearing capacity required.
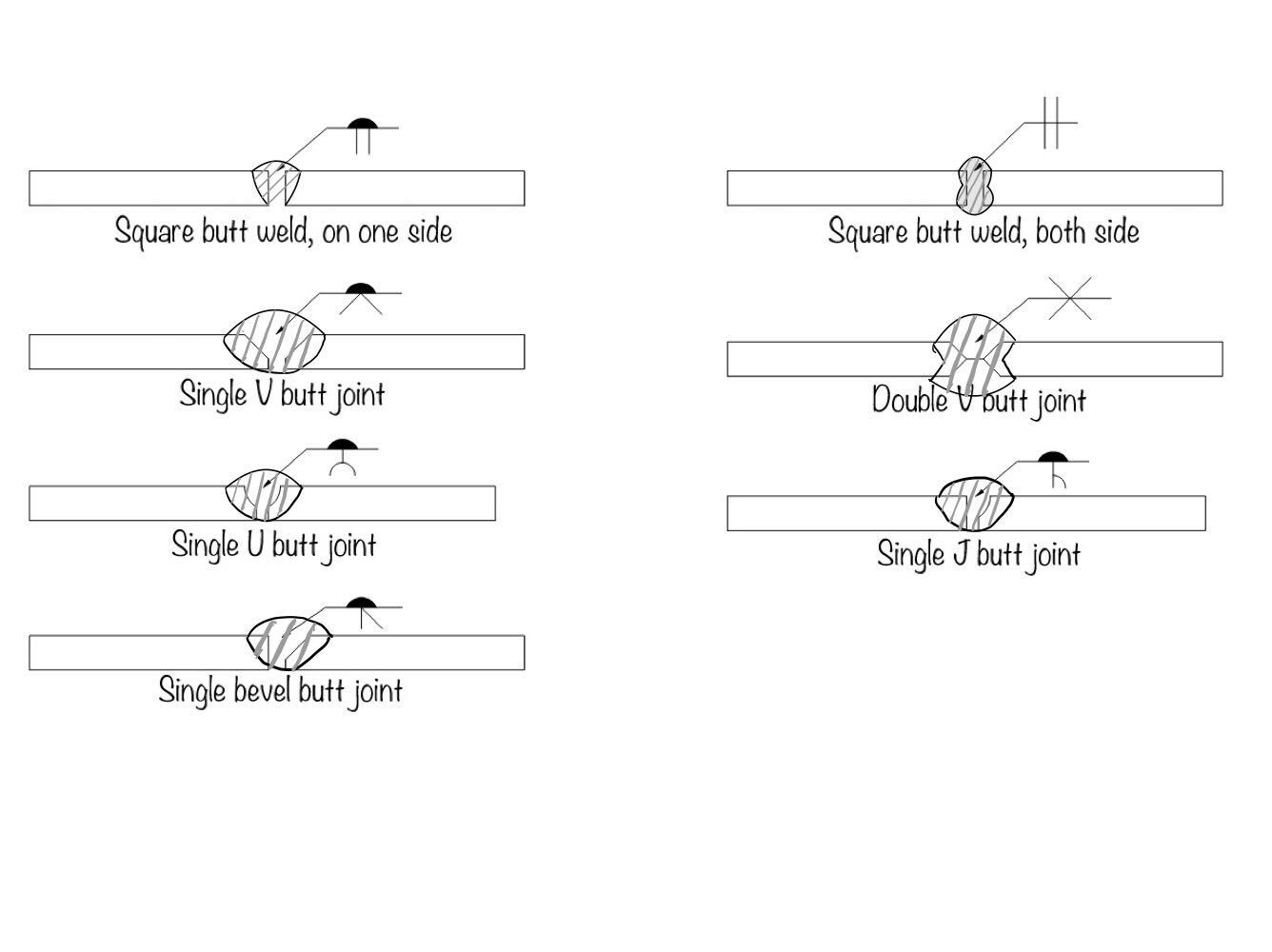
Fillet weld
Fillet welds are often used to join two members that are in different planes. In comparison to butt welds, fillet welds are more prevalent because of their frequent application. Furthermore, these welds create a triangular shape between the two metal pieces, making them suitable for T-joints, lap joints, and corner joints.
Fillet welds require less surface preparation, making them easier to create. However, they are not as strong as groove welds and may lead to stress concentration. Fillet welds are typically preferred in lightly stressed members where design stiffness is prioritized over strength, and different types of fillet welds can be seen below.
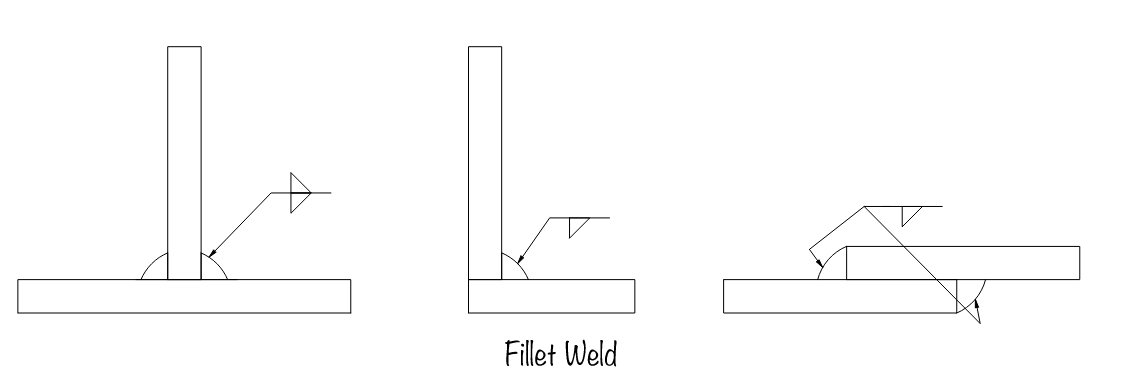
Slot Weld and Plug Weld
When the length of a fillet weld cannot meet the necessary requirements, slot and plug welds are employed as supplementary measures.
- Slot Weld: In this method, a plate with a circular hole is placed on the plate to be joined, and a fillet weld is created along the circumference of the hole.
- Plug Weld: Small holes are created in one plate and placed over the other plate to be connected, after which the holes are filled entirely with filler material.
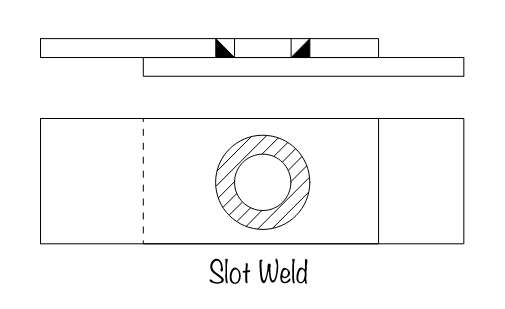
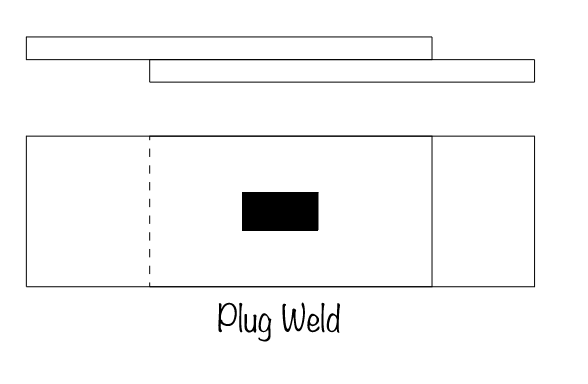
Tack Weld
It is a type of weld to temporarily hold two pieces of metal together before a permanent weld. Tack welds are typically small and can be easily removed once the permanent weld is completed.
Spot Weld
Spot welding is a type of weld used to join two or more pieces of metal by applying pressure and passing an electric current through them. Use of this type of weld is common in the automotive industry to join sheet metal components.
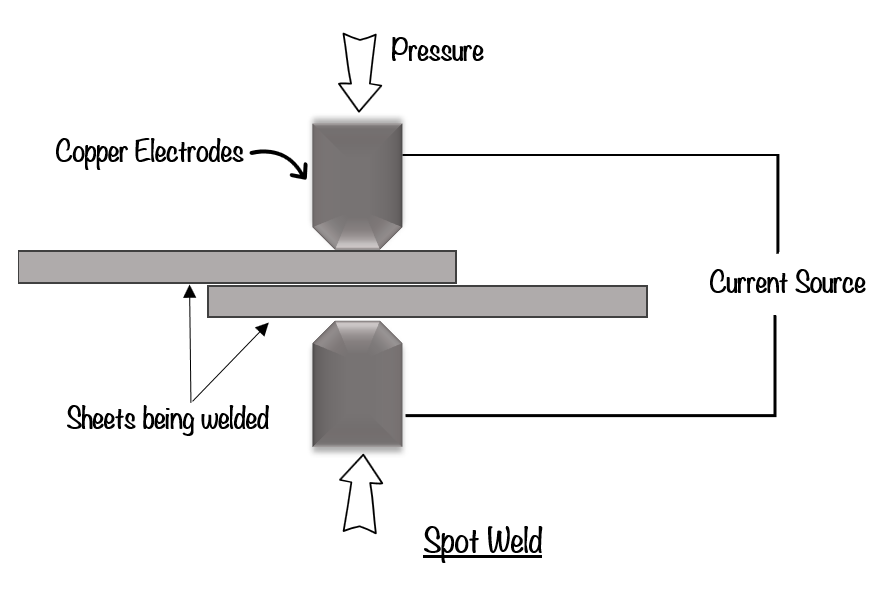
Conclusions
This post provides an overview of the various welding techniques used in industries today. Moreover, the article gives a comprehensive overview of the different types of welded joints and their applications, highlighting the significance of welding as a critical process in various industries. Overall, this post presents a detailed insight into welding and its diverse applications in modern-day industries.
To summarize, the key takeaways are:
- Welding: It is a process to join two or more metal pieces.
- Different types: There are several different weld joints available, including butt welds, fillet welds, plug welds, and many others. Each weld joint has its advantages and disadvantages, making it suitable for specific applications.
- Application: The factors that influence the choice of joint, such as the type of material being weld, the thickness of the material, and the load-bearing capacity required.
This article was crafted by a group of experts at eigenplus to ensure it adheres to our strict quality standards. The individuals who contributed to this article are:
Author
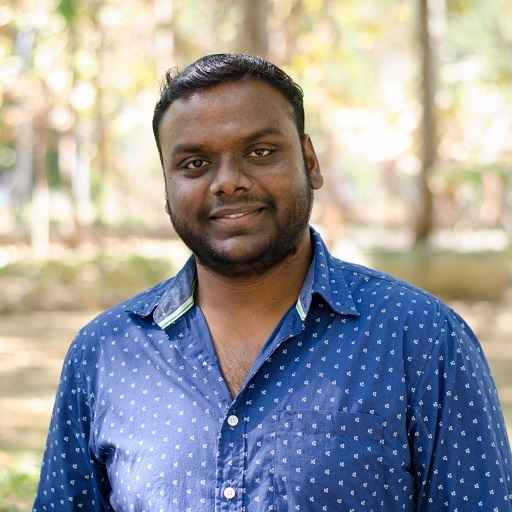
Sivraj
M.Tech
He is a research scholar working to get a doctorate in structural engineering.