The design of a pile foundation is a tedious process. It involves lots of components to be designed. Before this, we discussed different types of deep foundations and the construction stages of pile construction. In this article, we will discuss the different steps involved in the pile foundation design. We will also see the strut and ties model of the load transfer mechanism of the pile foundation.
Relevant code for pile foundation
Pile foundation can be made of many materials. We have discussed in the previous article of deep foundation we have seen the different types of material we can use to construct the piles. In this article we will focus on the concrete pile and we will discuss the design procedure of concrete piles.
Following Indian standard code can be referred to design the pile foundation:
- IS code 2911-2010
- Part-1 – concrete piles
- Section-1 -Driven cast in situ concrete piles
- Section-2 – Bored cast in situ concrete piles
- Driven precast concrete piles (revised-2010)
- Part 2 – timber piles
- Part 3 – Under reamed piles
- Part 4 – Load test on piles
- Part-1 – concrete piles
These are the Indian standard code which we must have to follow while we are designing the piles.
Basic design philosophy of the pile
Before designing pile we must have to understand the basic behaviour of the pile foundation.
Before that lets discuss the basic components of the pile foundations. Please look into the figure below. This figure shows the very basic elements of the pile foundation. This is the case of bridges. Large compression columns of the bridge is called piers. This pier is resting over the pile cap. This pile cap further transfer the load to the four piles below the pile cap.
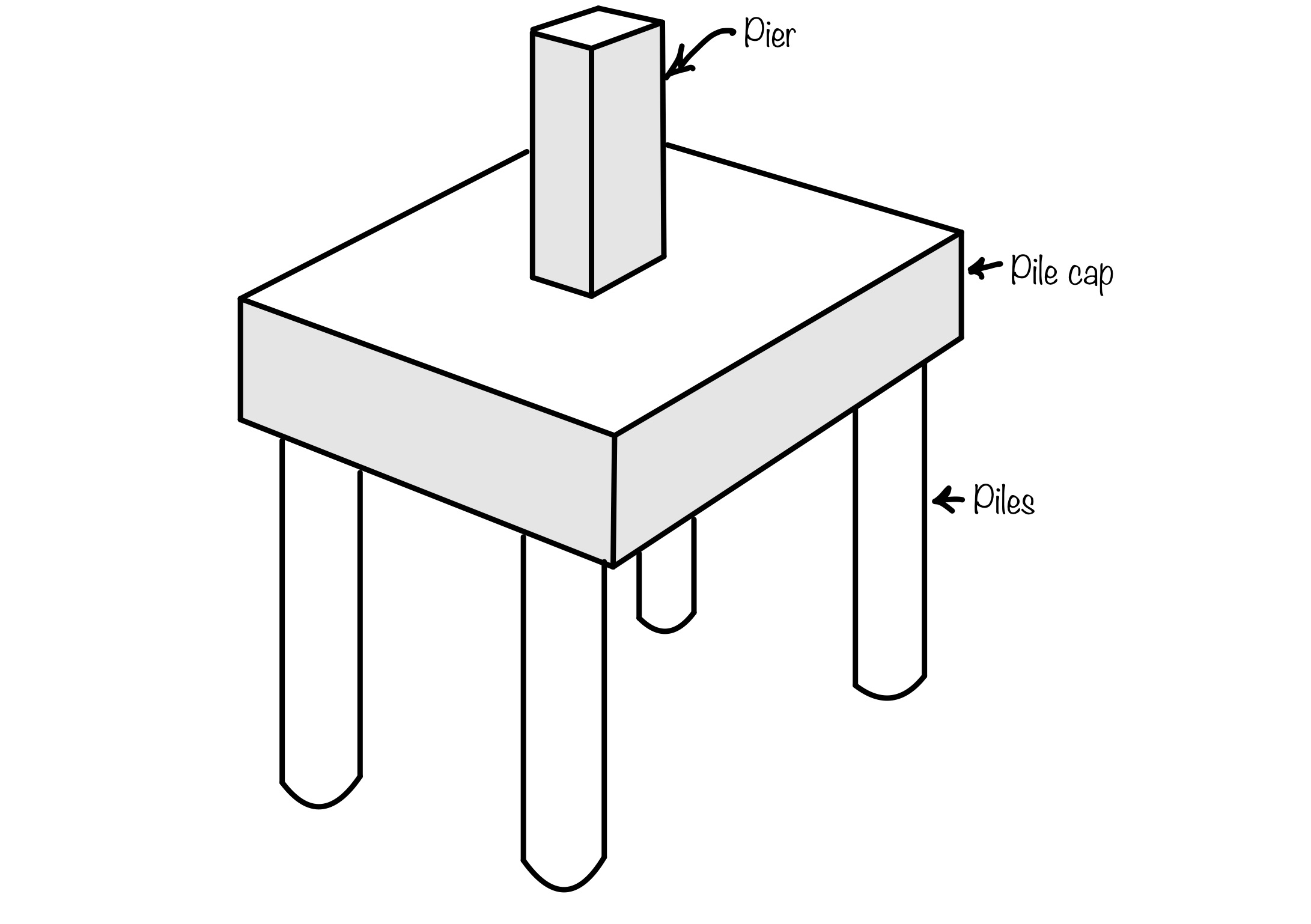
After getting the basic idea of the pile foundation its time to understand the behaviour of the pile foundation. When you see the figure below you can understand the load transfer mechanism in the pile foundation. The pier transfers the vertical load to the pile cap. This pile cap finally distribute the load from the pier to the four pile.
In the image below you can see the action of piles as column and the pile load reaction diagram.
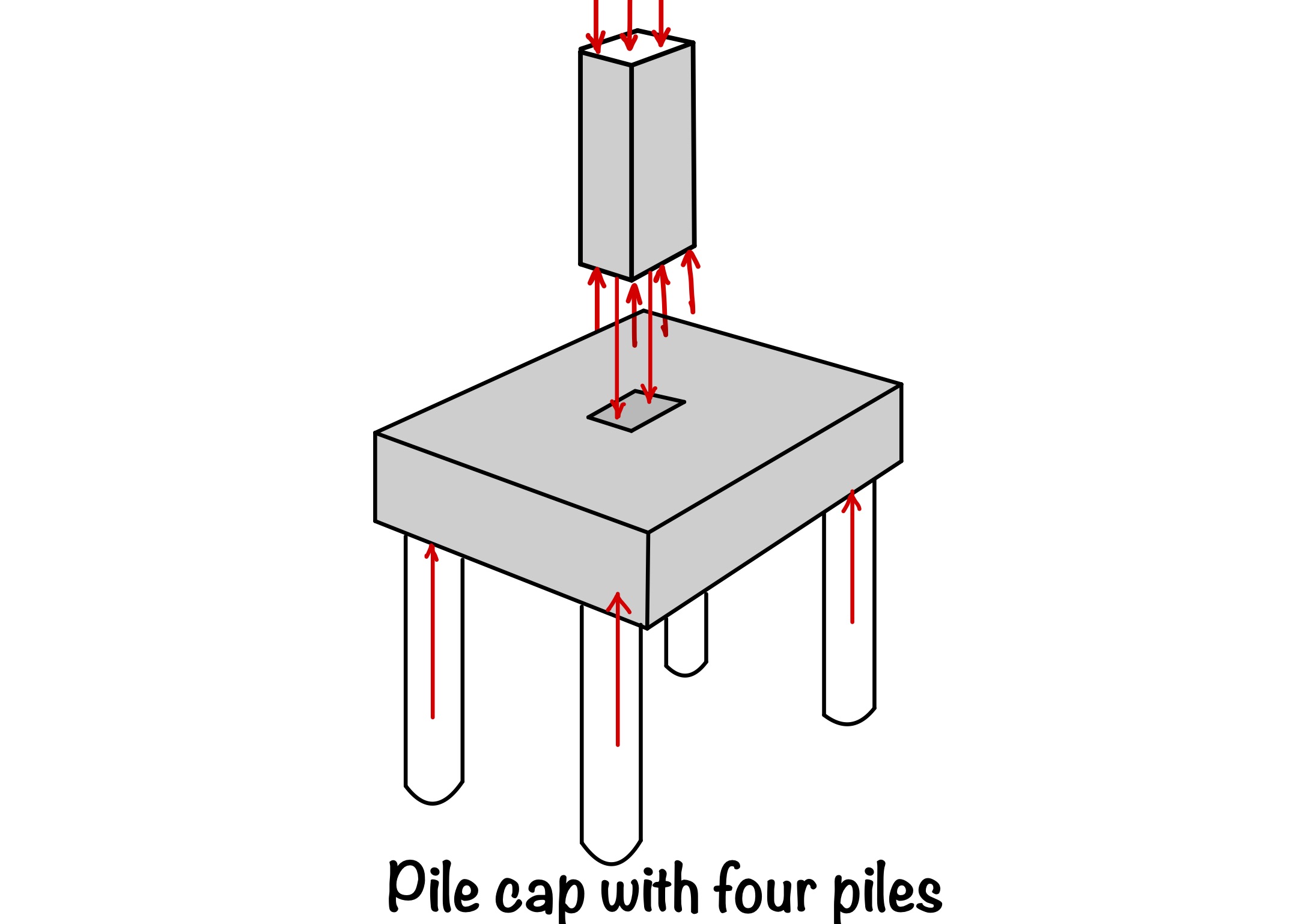
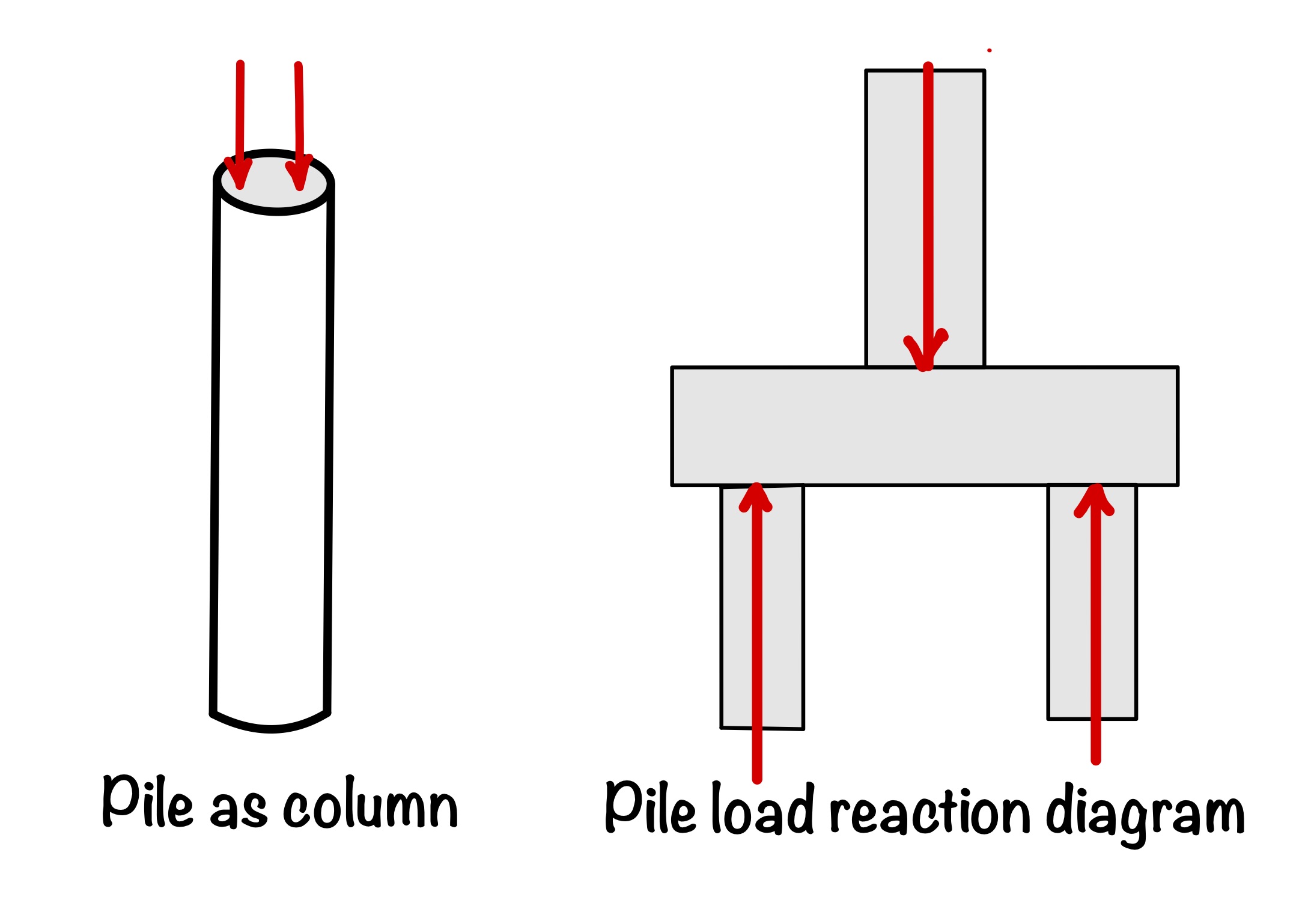
After this we now have to discuss the pile cap. The pile cap is acting like a slab (which resist the load by bending action). Please refer the figure below to have a feel about the pile cap behaviour.
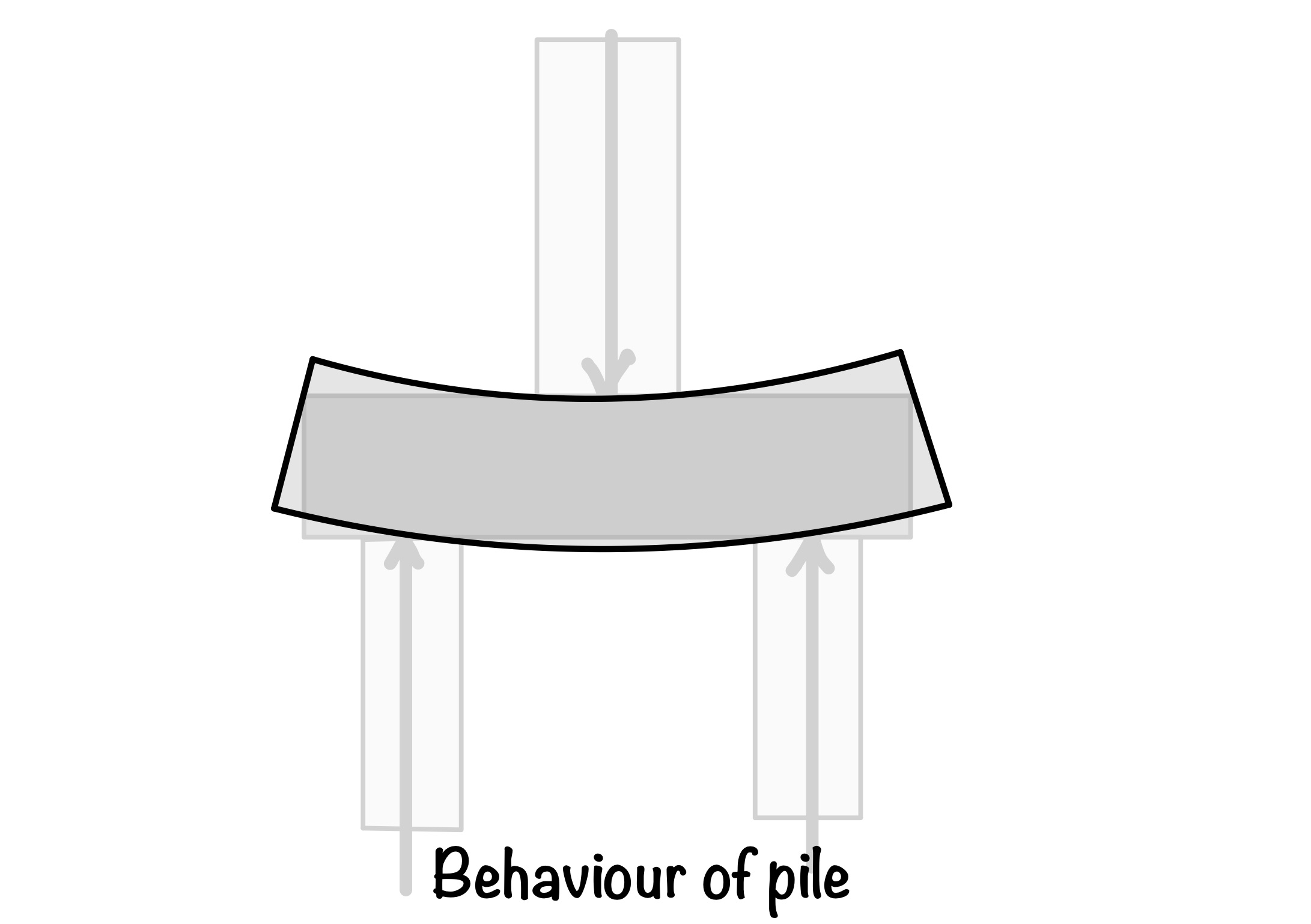
Piles in detail
In this section we will see the components of pile in detail. Please refer the figure below.
As you know we are discussing the concrete piles here. As the first step we make the pile hole and than pour the the concrete with the reinforcements. We cast the pile upto ground level.
Now after this we cut the some portion of the the concrete pile. The length upto which we are removing the concrete we call it chipped off length as shown in figure. After this we place the levelling course on lean concrete and then we tie the reinforcement for the pile cap. After the reinforcement we place the shuttering and then casting of pile cap.
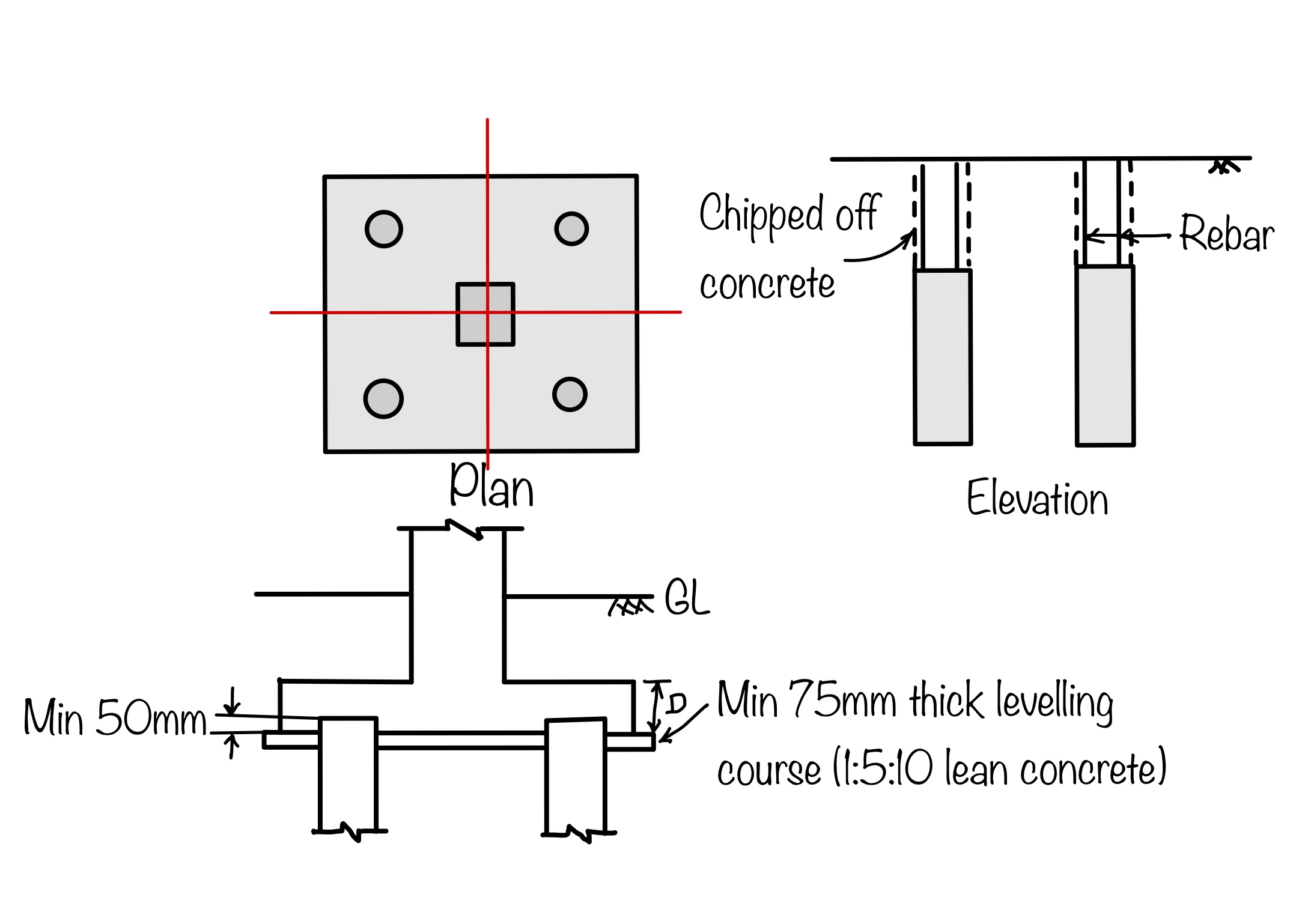
Design of Piles
As the first step of the design we will design the piles. We have already discussed that pile behave as the column. Hence we will design it as the column.
These are the following steps to design the pile:
- Longitudinal reinforcement: In the first step we will see the how to calculate the area of longitudinal reinforcement required in the pile.
- Use IS-456:2000 – Clause 39.4 (For axially loaded members)
Using this formula we can calculate the area of steel required in the pile.
We have to keep eye on the minimum reinforcement mentioned by the IS code is $0.4\%$ throught out the section (cast in situ). The number of bars are restricted to 6 and diameter of bar is 12 mm.
Minimum reinforcement for the precast pile is mentioned in the IS 2911 Part-1 section 3. This has to follow the condition mentioned below.
- $1.25\%$ of cross section area for $l< 30D$.
- $1.50\%$ of cross section area for $30 D \le l \le 40D$.
- $2.00\%$ pf cross section area for $l\ge 40D$.
After calculation of longitudinal reinforcement now we have to calculate the lateral reinforcement.
Lateral reinforcement of pile
We have to keep following things in mind while providing the lateral reinforcement in the pile.
- The diameter and spacing of the same is chosen to impart adequate rigidity of the reinforcing cage during its handling and installations.
- The minimum diameter $\ge 8$ mm and the spacing $\ge 150$ mm.
- Stiffner rings – Minimum dia $16$ mm at $1.5$ m c/c.
After the reinforcement we also need to check the concrete which we are going to use in pile.
These are the few points which we have to take care while doing concreting of piles:
- The slump should be $150$ to $180$ mm at the time of pouring.
- The \textbf{minimum grade} of concrete – M25
- Minimum cement content 400 kg/cum, never less than 350 kg/cum
In the steps which we have discussed above we have calculated the material needed to cast the pile. As you know casting of pile is also very difficult hence we need to take measures about this also.
These are the few points which we need to follow:
- For vertical pile max angular deviation of $1.5\%$ and for raker pile $4\%$.
- Pile should not deviate more than 75 mm or D/6 (whichever is less).
- For a single pile – 50 mm or D/6 (whichever is less) [100 mm for pile dia 600 mm ]
Design of pile cap
After designing the pile we need to design the pile cap. The pile caps are designed for the bending action. The main function of the pile cap is to disburse the load coming from the pier or column to the piles.
To understand this we please refer to the figure below.
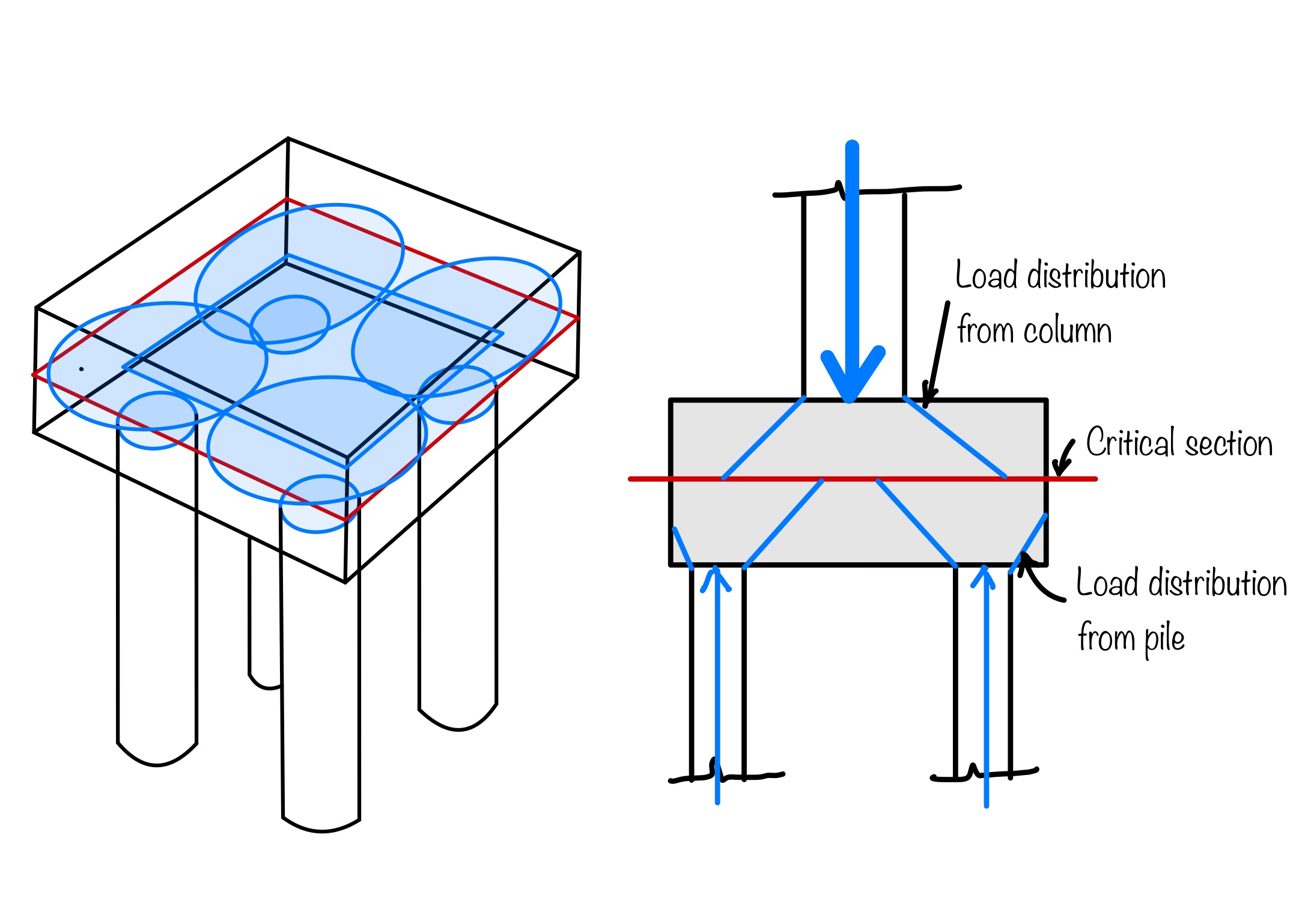
The yellow arrow shows the load coming through the pier or columns. The pile can distribute this load to the piles as shown in figure. The red line in the figure shows the critical plane as shown in figure.
We generally assume the distribution of load is at $45^\circ$. Hence, our all calculations are based on this philosophy as shown in the figure. We are going to use this philosophy in the design of pile cap.
Geometry of pile cap of pile foundation
As we want to design the pile cap of the pile foundation we need to fix the geometry of the pile cap.
For this following steps needs to be followed:
- We need to calculate the spacing of the piles. In Clause 6.6 of IS 2911:2010, section -1 of the part-1 we can get the specifications for the piles. Which says as follows:
- 2.5 times diameter of piles if it is end bearing piles
- 3 times diameter of pile if it is friction pile
- After the size of the pile next step is to decide about the grouping of the piles.
- If you are providing the single pile then you can have to provide the grade beams in two direction.
- If you have more than 3 piles than pile head must be fixed.
These are the steps which helps you in fixing the geometry of the pile cap.
There are a few general criteria which you have to follow:
- Design criteria is similar to IS 456
- Rigid pile cap
- Consequential moment
- Cast over 75 mm thick levelling course of concrete
- Clear cover shall not be less than 60 mm
- Embedment of pile into cap should be 75 mm
- Design of grade beam IS 2911 Part 3
How to decide thickness of pile cap?
As you can see in the previous sections we have decided the basic geometry of the pile cap. We have also discussed the basic design considerations from IS-456:2000.
In this section we will see what are the parameters we need to check, for deciding the thickness, reinforcement, development length etc. of pile cap.
Important criteria for pile cap design are as follows:
- One way shear (Column load transfer)
- Two way shear (Column load transfer)
- One way shear (Pile reaction transfer)
- Two way shear (Pile reaction transfer)
- Load transfer from column to pile cap (development length)
- Load transfer from pile to pile cap (development length)
- Flexural action (flexural reinforcement)
We will see each criteria individually.
Oneway shear for column
We have to transfer the load coming from the column to ground through the pile cap. As you can see in the figure below that the cross section of pile at a distance $d$ from the column face becomes the critical section for the one way shear check.
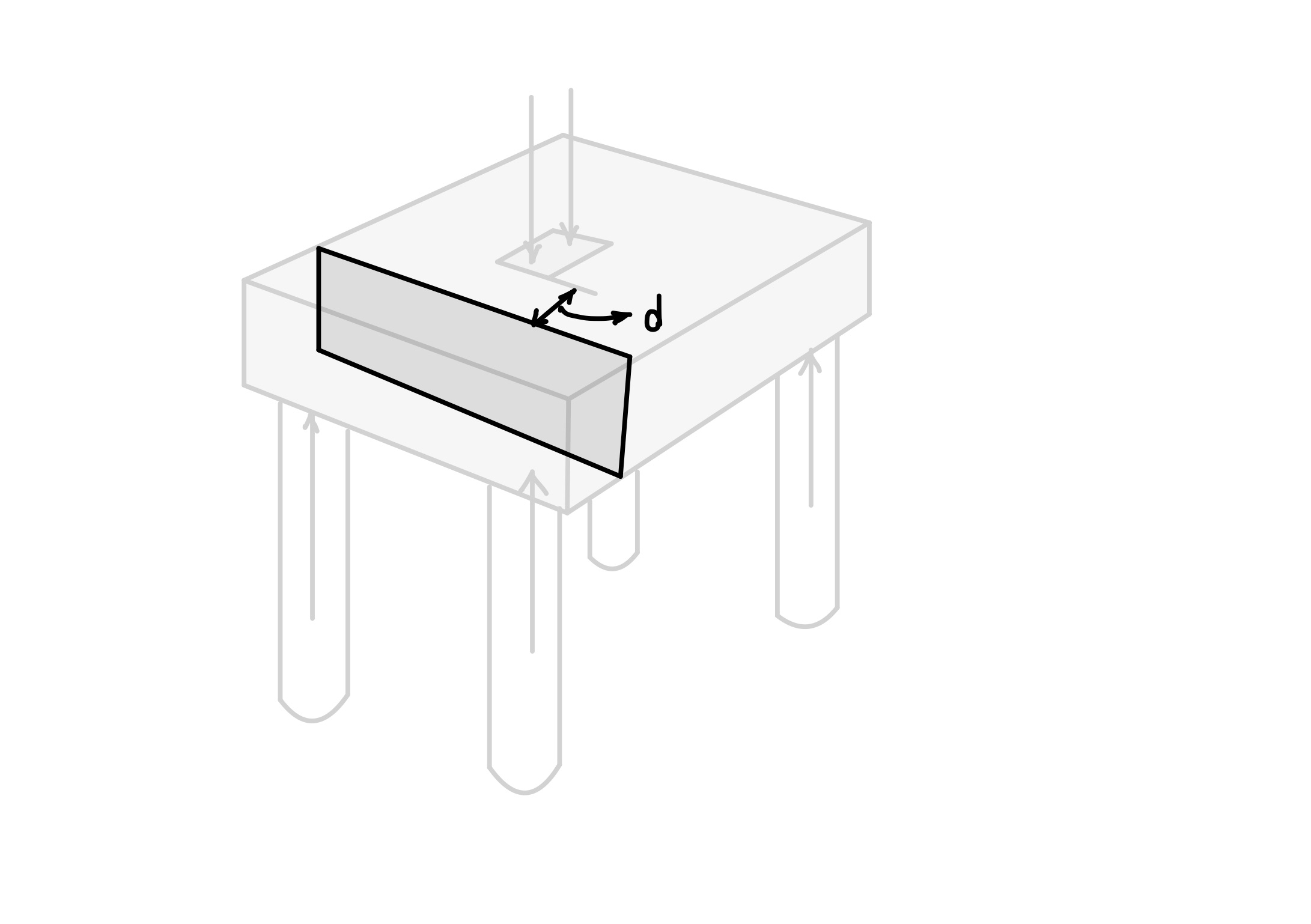
As we know that the reaction in the footing is coming only from the piles not from the entire footing. We have to take care that whether the piles are inside the critical section or outside the critical section.
So, again code solved this issue, according to clause $34.2.4.2$ of IS-456:2000 it says:
- $D_p/2$ outside this distance – entire pile reaction is taken into consideration, where $D_p$ is the diameter of the pile.
- And for the other position we have to perform the linear interpolation as shown in the figure.
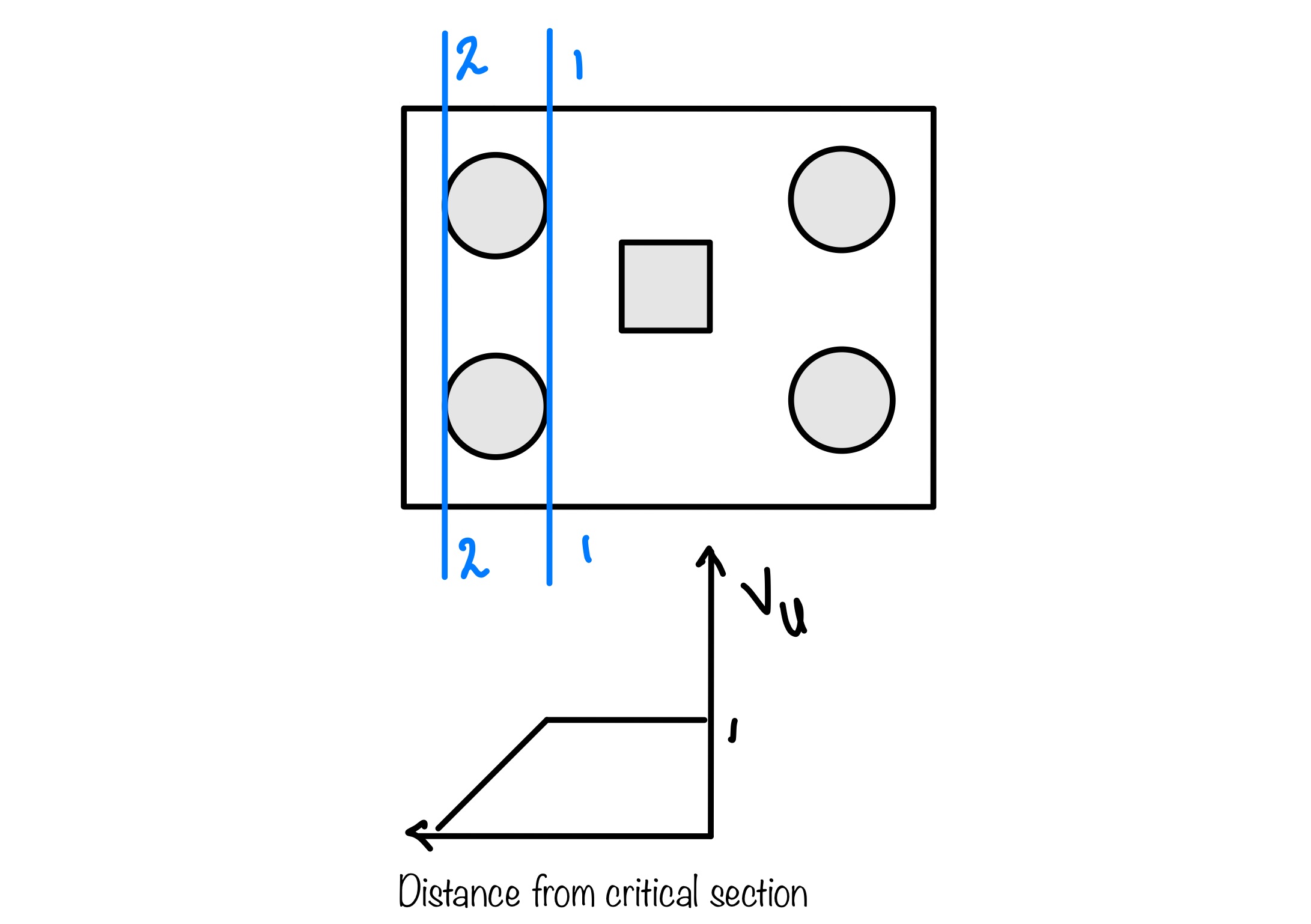
Two shear for the column
When we consider the design for two-way shear the critical section will be as shown is the figure. The area of the cross-section of the critical section bears the shear force.
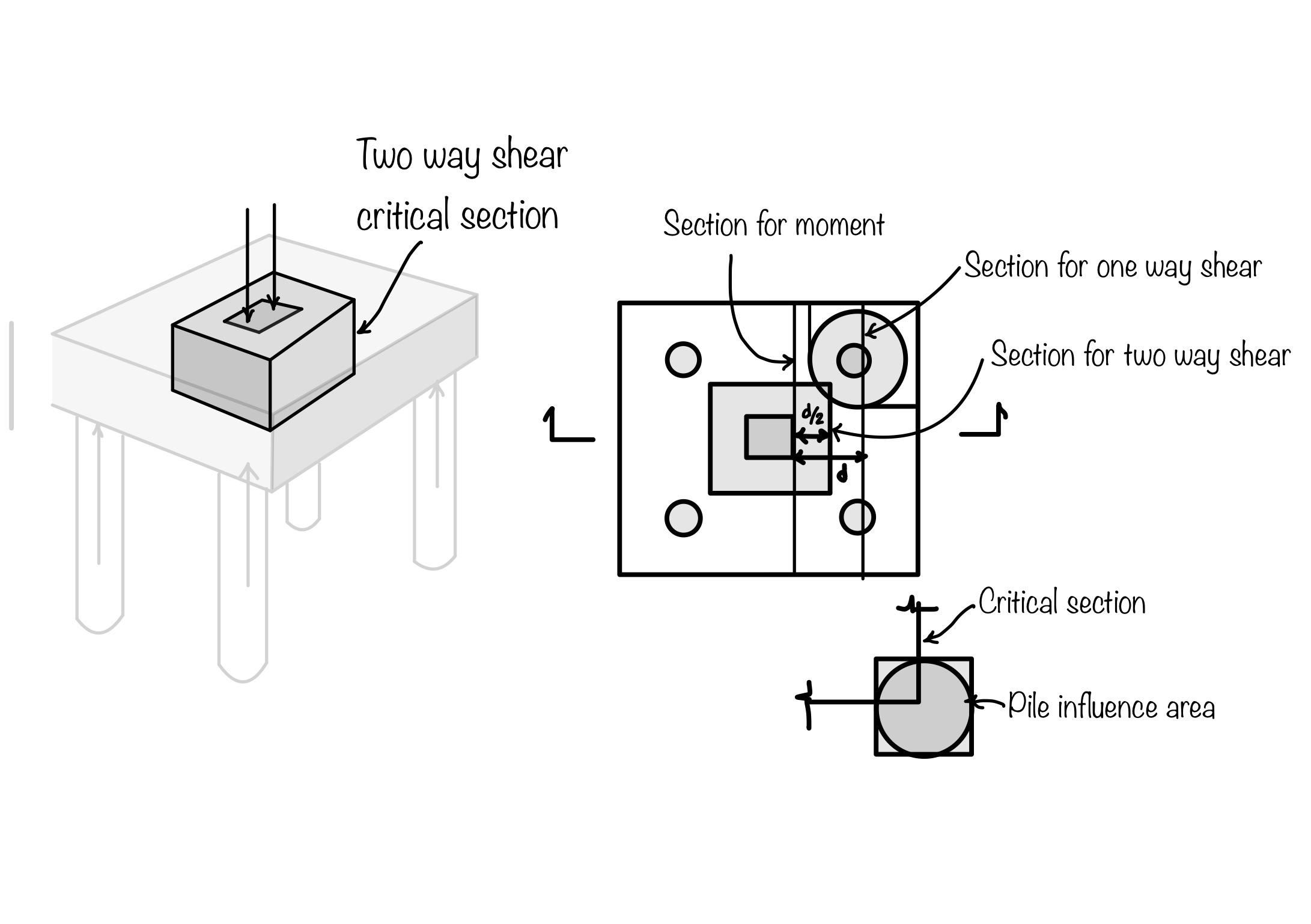
The second part of the figure shows the critical section for the two way shear in the plan view. There are two loads one which is coming from the pier and one which is coming from the pile. The critical section for the pile and pier both are shown in the figure.
You can also check the critical section for the bending or flexure action pile cap. The critical section for the bending will be just at the face of the column. Which you can see in the figure.
After identifying the critical sections for different types of actions we can calculate the resistance provided by the particular section. To increase the resistance capacity of the section now we can provide the reinforcement.
Reinforcement in the pile caps
In this section, we will see the different types of reinforcement in the pile cap. The figure below shows the reinforcement details of the pile cap. The bar coming from the piers should be continued to bear the high shear force. Hence we provide the development length $L_d$ to the bars.
A clear overhang of $100$ to $150$ mm is generally provided in the pile cap as you can see in the figure. The bottom reinforcement should be placed at the cover of $75$ mm to develop the bond length we need to provide the development length to these bars also.
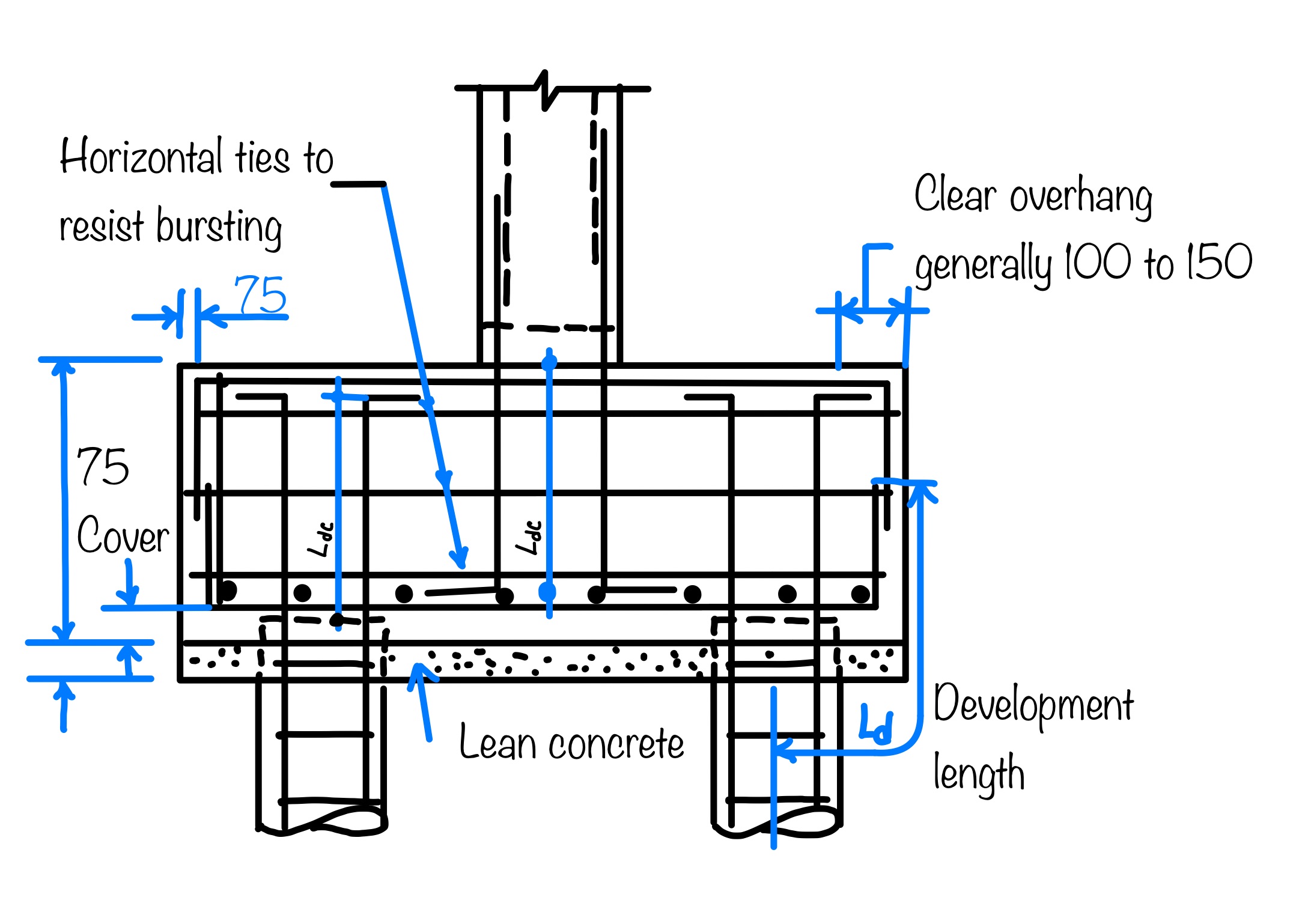
Strut and tie model for the load distribution of the pile cap
Another theory of load distribution is the strut and tie model. If you recall our previous discussion you can recall that the strut is the compression member. The piers transfer the load through the strut and then the strut transfers the load to the piles as shown in the figure. The piles take care of the vertical load of the strut, but the horizontal component of the strut ties comes into the picture.
The figure below shows the strut and ties model of the load transfer mechanism.
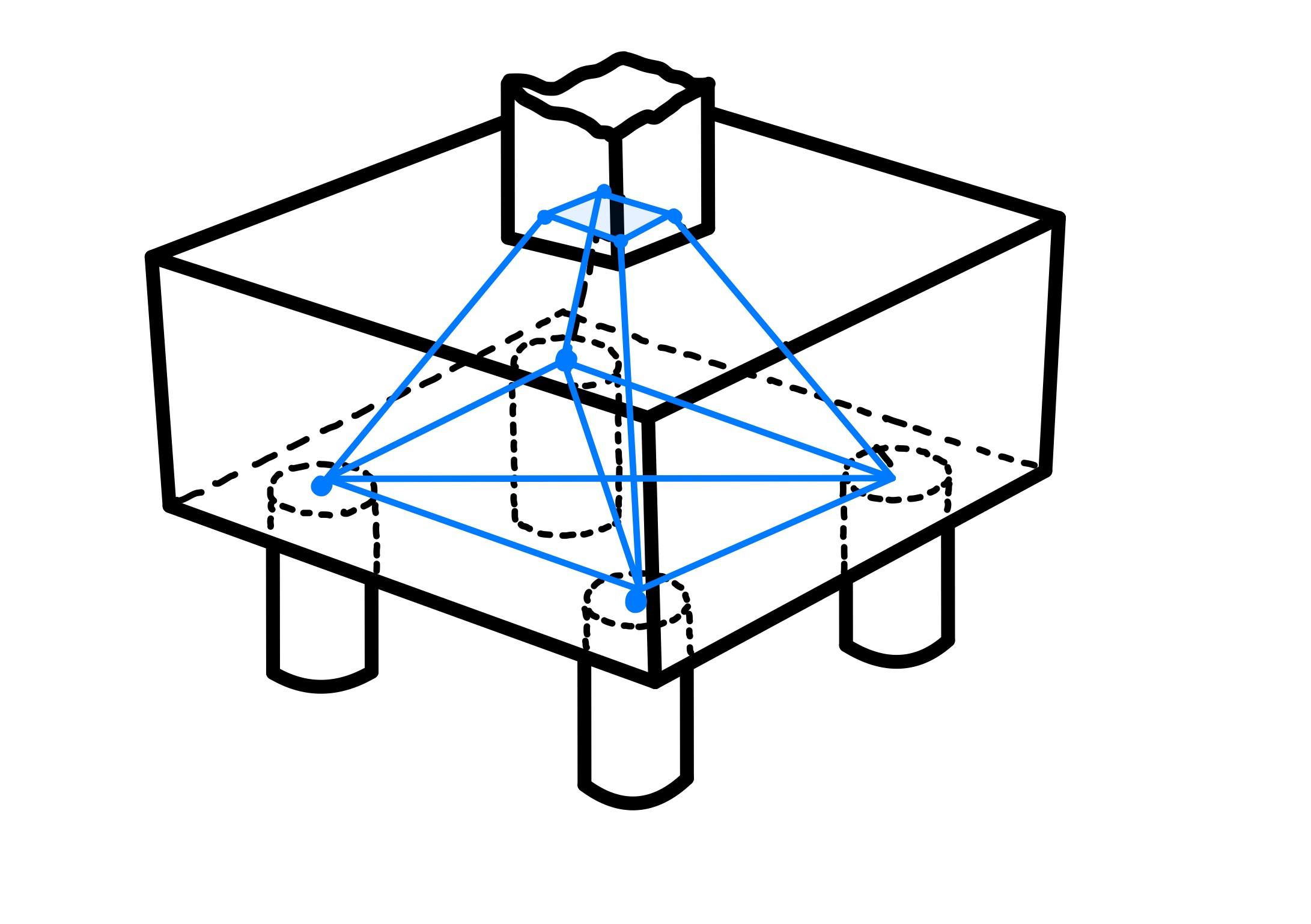
Conclusion
In this article you have learned the following key points:
- Design: We have also discussed the different steps involved in designing of the pile.
- One-way shear: We have discussed the area which resists the one-way shear in the article.
- Two-way shear: The two-way shear by pile and piers we have seen in the article and also discussed the critical section responsible for this.
- Strut and tie model: We have discussed the strut and tie model mechanism of the load transfer in the pile.
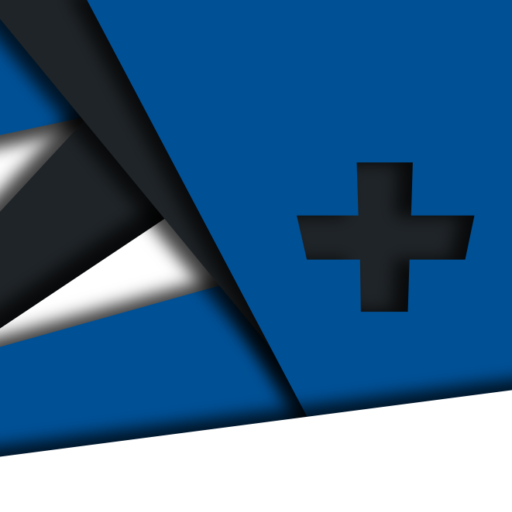
Android Apps
⭐️ ⭐️ ⭐️ ⭐️ ⭐️ 1000+ | 400,000 + Downloads (Cumulative)
At eigenplus, our goal is to teach civil engineering students about structural analysis and design starting from the fundamental principles. We do this with the help of interactive android applications and accompanying web articles and videos.
Our apps have helped more than 400 thousand students across the world to understand and learn the concepts of structural engineering. Check out our apps on the google play store.
This article was crafted by a group of experts at eigenplus to ensure it adheres to our strict quality standards. The individuals who contributed to this article are:
Author
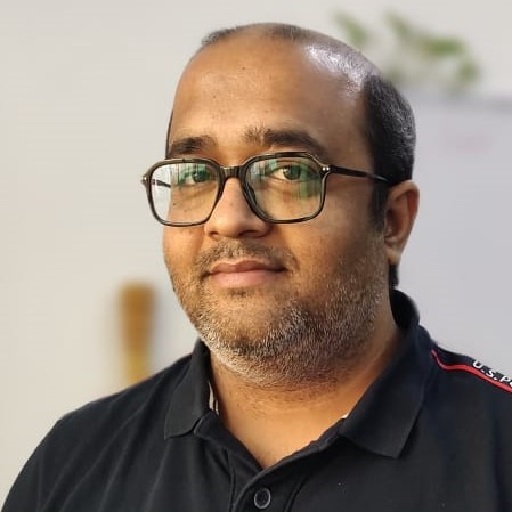