In the previous articles, we have seen design examples for I-section column where we discussed that the design steps cannot be applied for single angle struts. So, what makes single-angle sections special? How to design a single-angle compression member? Don’t worry. The steps to determine the design compressive strength of a single angle are similar to that of an I-section column except for few changes. Let us look into those in detail below.
Why single-angle compression members are not designed as I-section column?
As discussed in the article “Column | Design strength calculation by an example”, the design compressive stress $f_{cd}$ for an I section columns as per IS 800:2007:
$$ f_{cd}=\frac{f_y/\gamma_{m0}}{\phi+[\phi^2-\lambda_e^2]^{0.5}}=\chi f_y/\gamma_{m0}\leq f_y/\gamma_{m0} $$
where,
$\phi=0.5[1+\alpha(\lambda-0.2)+\lambda^2]$
$\alpha=$ Imperfection factor given in Table 7, IS 800:2007
$\lambda_e=$ non-dimensional effective slenderness ratio $=\sqrt{f_y/f_{cc}}$
$f_{cc}=$ Euler buckling stress $=\frac{\pi^2E}{(KL/r)^2}$
$\chi=$ Stress reduction factor given in Table 8 IS 800:2007
$\gamma_{m0}=$ Partial safety factor for material strength $=1.1$ (from Table 5, IS 800:2007)
The calculated value for different buckling class is given in Table 9, IS 800:2007.
Here, $f_{cc}$ used to compute non-effective slenderness ratio $\lambda_e$ is Euler buckling stress. The Euler (read as oiler) buckling stress have limitations and therefore is applicable to doubly-symmetric (I-section) or singly-symmetric (Channel) sections. However, it is not applicable to unsymmetric sections such as single angles. What to do in such a case?
Equivalent slenderness ratio for single angle strut
Clause 7.5.1.2, IS 800:2007 deals with the scenario when Euler buckling stress is not applicable and there exists no axes of symmetry. The clause asks the designer to use an equivalent slenderness ratio in place of non-effective dimensionless slenderness ratio $\lambda_e$. This is given as:
$$ \lambda_e=\sqrt{k_1+k_2\lambda_{vv}^2+k_3\lambda_{\psi}^2} $$
where,
$k_1, k_2, k_3 =$ Constants depending upon the end conditions given as per Table 12, IS 800:2007
$$ \lambda_{vv}=\frac{(\frac{l}{r_{vv}})}{\epsilon\sqrt{\frac{\pi^2E}{250}}} \quad and \quad \lambda_{\phi}=\frac{(b_1+b_2)/2t}{\epsilon\sqrt{\frac{\pi^2E}{250}}} $$
where,
$l=$ centre-to-centre length of supporting member
$r_{vv}=$ radius of gyration about the minor axis.
$b_1,b_2=$ width of the two legs of the angle
$t=$ thickness of the leg, and
$\epsilon=$ yield stress ratio $= (250/f_y)^{0.5}$
Step-by-step procedure using a design example
Problem: Determine the design compressive strength of ISA 100 mm $\times$ 100 mm $\times$ 6 mm of grade Fe410 used as a strut in roof truss. The strut is welded at each end and the length between two ends is 3.50 m. Assume gusset member fixity as fixed condition.
Step 1: Determine the cross-sectional area $A$, minimum radius of gyration $r_{vv}$ for the angle section from IS handbook SP: 6(1).
For the given problem,
$$ A=1167 \; mm^2 \quad and \quad r_{vv} = 19.5\; mm $$
Step 2: Determine constants $k_1, k_2,\; and \; k_3$ using Table 12, IS 800:2007.
For the given problem, the ends are welded and the gusset plate is fixed. Thus, using Table 12, IS 800:2007
$$ k_1= 0.20\quad k_2=0.35\quad k_3=20 $$
Note: For welded ends conditions use the scenario “No. of Bolts at Each End Connection $\ge$ 2” case in Table 12, IS 800:2007.
Step 3: Determine the equivalent slenderness ratio $\lambda_e$ as per Clause 7.5.1.2, IS 800:2007.
The equivalent slenderness ratio, $\lambda_e$ is given as:
$$ \lambda_e=\sqrt{k_1+k_2\lambda_{vv}^2+k_3\lambda_{\psi}^2} $$
For the given problem,
$$ \lambda_{vv}=\frac{(\frac{l}{r_{vv}})}{\epsilon\sqrt{\frac{\pi^2E}{250}}}=\frac{3500/19.5}{\sqrt{\frac{250}{250}}\sqrt{\frac{\pi^2\times 2\times 10^5}{250}}}=2.02 $$
$$ \lambda_{\phi}=\frac{(b_1+b_2)/2t}{\epsilon\sqrt{\frac{\pi^2E}{250}}}=\frac{(100+100)/(2\times 6)}{\sqrt{\frac{250}{250}}\sqrt{\frac{\pi^2\times 2\times 10^5}{250}}}=0.188 $$
Using $k_1, k_2,\; and \; k_3$ from Step 2, we have
$$ \lambda_e=\sqrt{k_1+k_2\lambda_{vv}^2+k_3\lambda_{\psi}^2}=\sqrt{0.75+0.35\times (2.02)^2+20\times (0.188)^2}=1.528 $$
Step 4: Determine the design compressive stress, $f_{cd}$ as per clause 7.1.2.1 IS 800:2007 using the calculated $\lambda_e$
$$ f_{cd}=\frac{f_y/\gamma_{m0}}{\phi+[\phi^2-\lambda_e^2]^{0.5}}=\chi f_y/\gamma_{m0}\leq f_y/\gamma_{m0} $$
where,
$\phi=0.5[1+\alpha(\lambda_e-0.2)+\lambda_e^2]$
$\alpha=$ Imperfection factor given in Table 7, IS 800:2007 $=0.49$ for single angle sections.
Here for the given problem,
$\phi=0.5[1+\alpha(\lambda_e-0.2)+\lambda_e^2]=0.5[1+0.49(1.528-0.2)+(1.528)^2]=1.992$
Hence,
$$ f_{cd}=\frac{f_y/\gamma_{m0}}{\phi+[\phi^2-\lambda_e^2]^{0.5}}=\frac{250/1.1}{1.992+[1.992^2-1.528^2]^{0.5}}=69.05\; MPa $$
Step 5: Calculate the design compressive strength $P_d=A\times f_{cd}$
Hence,
$$ P_d=1167 \times 69.05=806\; kN $$
Conclusions
The following are the key points to remember from the article:
- Asymmetric: Asymmetric single-angle sections undergo flexural torsional buckling, unlike I-sections which undergo flexural buckling.
- Design compressive strength: The Table 9 of IS 800:2007 cannot be used for single-angle sections to determine the design compressive strength $f_{cd}$ . We need to calculate manually the effective non-dimensional slenderness ratio and feed into the Clause 7.1.2.1 of IS 800:2007.
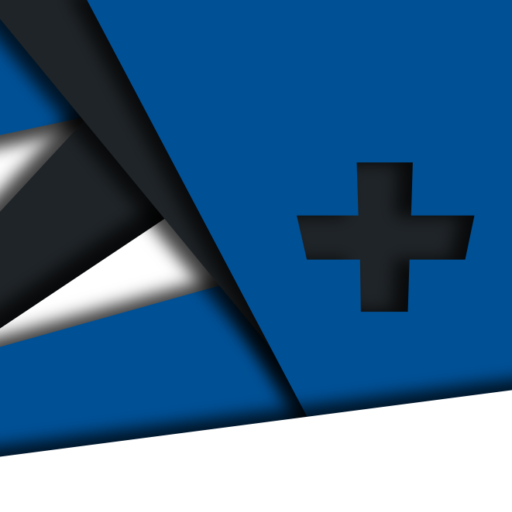
Android Apps
⭐️ ⭐️ ⭐️ ⭐️ ⭐️ 1000+ | 400,000 + Downloads (Cumulative)
At eigenplus, our goal is to teach civil engineering students about structural analysis and design starting from the fundamental principles. We do this with the help of interactive android applications and accompanying web articles and videos.
Our apps have helped more than 400 thousand students across the world to understand and learn the concepts of structural engineering. Check out our apps on the google play store.
This article was crafted by a group of experts at eigenplus to ensure it adheres to our strict quality standards. The individuals who contributed to this article are:
Author
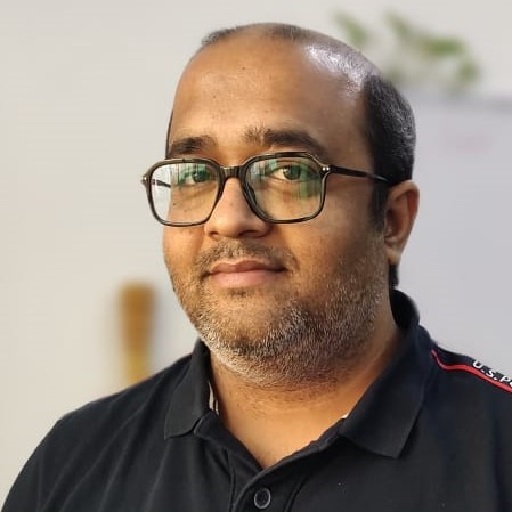