Introduction
Some time we call it as “Strength of material” also. In this post we will understand why it is called so. What are the objective of this course and what are the prerequisites for this course.
As the name suggest the strength of material means we will be finding the strength of materials. We have tried to answer your most probable question which may arise while thinking about the strength of material.
what is the strength?
Strength is defined as the stress just before failure. So, it is the maximum stress that any material can take just before the failure.
How do we know that material is at failure?
Failure of any material is given by the failure theories. After failure point we have to know the
What is state of stress, and how to find the state of stress?
Although its too early to discuss all this things. But it will give you the complete picture of the subject. State of stress means knowing all the components of stress at a point. To properly understand this you need to go through the concepts of stress, strain.
How we apply stress in the material?
Sorry to again disappoint you, but you can not apply the stress. It is the hypothetical quantity which physically does not exists. You can apply the force in the material. This force in the material will create strain in the material. This strain ultimately give rise to stress.
What are the different forces which creates stress in the material?
We classify the forces according to the resistance action by the material. Like the axial tension, compression are the forces which create extension and shortening in the material. Transverse forces causes bending of member, and torsion causes twisting. These all forces generates different kind of stress.
Let’s look the different type of forces and the members:
- Tensile force: Acts in the axial direction. It tries to extend the member. The name of the members who takes the tension is bars.
- Compression force: It is also axial force but opposite to tension it creates compression in the members. You can call them columns. We categories the long and short column. The short columns fails in the crushing while the long columns fails in buckling. .
- Transverse force: Transverse forces in the members are being resisted by the flexure action. We generally call them beams. Transverse forces generate bending moment and shear forces in beams.
- Torsion: When we apply twist in any member it rotates in its own axis. We call these members shaft.
can we add all the stresses to find the cumulative action?
We can not simply add the stress like the scalar quantities. Because stress is the tensor quantity. So although it may appear in the same direction but they might create different effect in the material.
How to know the resultant state of stress?
To know the state of stress at a point due to different stresses we must go through stress transformation. Also known as analysis of stress. This analysis gives the maximum and minimum stress and the plane on which it is acting. After
Solid
A material is called solid if in addition to normal force it can also support substantial shear force in a static condition. On the other hand, fluids cannot support shear force and have continuous deformation on the application of shear.
Force
It is an action that tends to maintain or alter the motion of a body or to distort it. The concept of force is commonly explained in terms of Newton’s three laws of motion set forth in his Principia Mathematica (1687). Force has both magnitude and direction, and thus, it is a vector quantity.
Deformation
Deformation refers to any change in the shape and size of the object due to an applied force or a change in temperature. Deformations could be elastic, where the object regains its shape on removal of the external force, or, could be plastic when the object is not able to regain its shape on removal of the external force.
Strain
Strain describes relative deformation or change in shape and size of elastic and plastic materials under applied forces. It is expressed as the ratio of total deformation to the initial dimension of the material body in which the forces are being applied.
Stress
Stress is the internal resistance offered by the material to the distorting effects of an external force. It is defined as the force across a “small” boundary per unit area of that boundary. If the body reaches the state of equilibrium then this resistance is equal to the applied load. Thus, stress becomes equal to the applied force divided by the area.
Principal Stresses
Principal stresses are the extreme values of the normal stresses possible in the material. These are the maximum normal stress and the minimum normal stress possible for a specific point on a structural element. Maximum normal stress is called major principal stress while minimum normal stress is called minor principal stress. Shear stress is zero where principal stress occurs.
Principal Strain
The principal strain is the extreme values of the normal strain possible in the material. These are the maximum normal strain and the minimum normal strain possible for a specific point on a structural element. The maximum normal strain we also call it major principal strain while minimum normal strain we call minor principal strain. Shear strain is zero where principal strain occurs.
Failure
Failure is the loss of load carrying capacity of the member. It could be due to fracture or permanent deformation beyond the operational range due to the yielding of the member. Failure theory is the science of predicting the conditions under which solid materials fail under the action of external loads.
Factor of Safety (FS)
It is the ratio of the Failure Load to the Working Load of the material unit. The purpose of using a factor of safety is to design the member in such a way that it can take FS times the load for which we design it. Essentially, the factor of safety is how much stronger the system is than it usually needs to be for an intended load. This takes care of the uncertainties in the assessment of loads while designing the member.
Conclusion
In the above post we tried to give you the complete picture of the strength of the material also know as “Solid Mechanics”. We have also discussed the some fundamental key concepts in the subject. To enjoy more of the learning you are suggested to code while understanding the subject. This will improve you understanding of the subject. We will start the python code series for strength of material to address this issue.
This course also have some prerequisites also. To have the proper understanding and joy of the course content you must go through the engineering mechanics and mathematics. We have also started the mathematics series from the engineers point of view.
Solid Mechanics
In this app, you would be able to explore the world of Solid Mechanics. The app covers many important topics in the field of solid mechanics.
- Interactive Mohr’s Circle of Stress and Strain.
- Calculators for Stress and Strain Analysis.
- Graphical representations of failure criteria.
- A detailed description of key concepts of Solid Mechanics with diagrams.
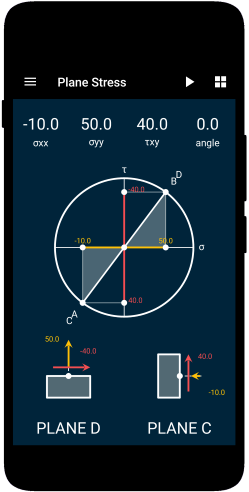
This article was crafted by a group of experts at eigenplus to ensure it adheres to our strict quality standards. The individuals who contributed to this article are:
Author
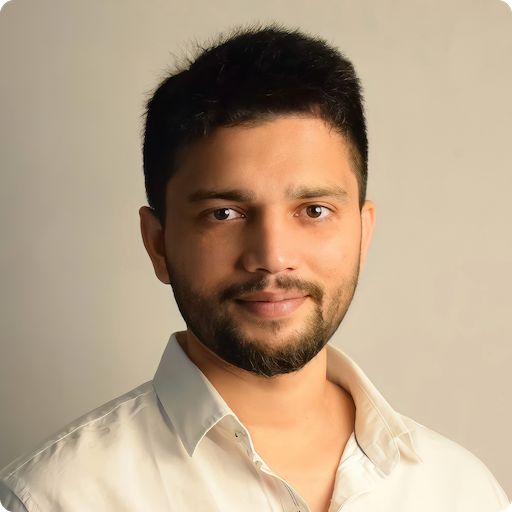
1 thought on “Fundamental Concepts in Solid Mechanics”