In the previous articles, we have seen design examples of finding the tensile strength of flat plate with Chain pattern bolting. In this article, let’s explore the difference for staggered bolting patterns.
What is the basic difference between chain bolting and staggered bolting?
The difference lies in the arrangement of the bolting. As the name refers, chain bolting is the simplest form of bolting where the number of bolts required to resist the forces are arranged in a series form. Any chosen row or column in the bolt group will have same number of bolts.
Whereas, in staggered bolting, the number of bolts required can be arranged in any shape such as diamond, star, rhombus.
Why is staggered bolting chosen?
For tensile members, the net area reduction due to bolt holes influences the design tensile strength due to rupture (Clause 6.3.1 IS 800:2007). In such a case, when the number of bolts requirement is higher and the dimension of connection length is a constraint, the bolts can be arranged in a staggered fashion to minimize the reduction of cross-sectional area.
Difference in design strength calculation: Determination of net-effective area
The only design strength calculation factor that changes from the usual design strength calculation of flat plates with chain bolting (refer to article XXYYZZ) is the determination of net effective area of cross-section.
As per IS 800:2007, for staggered bolting pattern,
$$ A_n=[b-nd_h+\Sigma\frac{p_{si}^2}{4g_i}]t $$
where,
$b, t=$ width and thickness of the plate respectively,
$d_h=$diameter of the bolt hole
$g=$ gauge length between bolt holes (centre-to-centre distance of the bolt measured perpendicular to the direction of applied load)
$p_s=$ staggered pitch length between bolt holes, as shown in figure below.
$n=$ number of bolt holes in the critical section
$i=$ subscript for summation of all the inclined legs
Step-by-step procedure using a design example
A flat plate, 300 ISF 8 mm of grade 410 is connected to a 12 mm thick gusset plate by 20 mm diameter bolts of grade 4.6. Calculate the design tensile strength of the member. The bolting pattern is shown below.
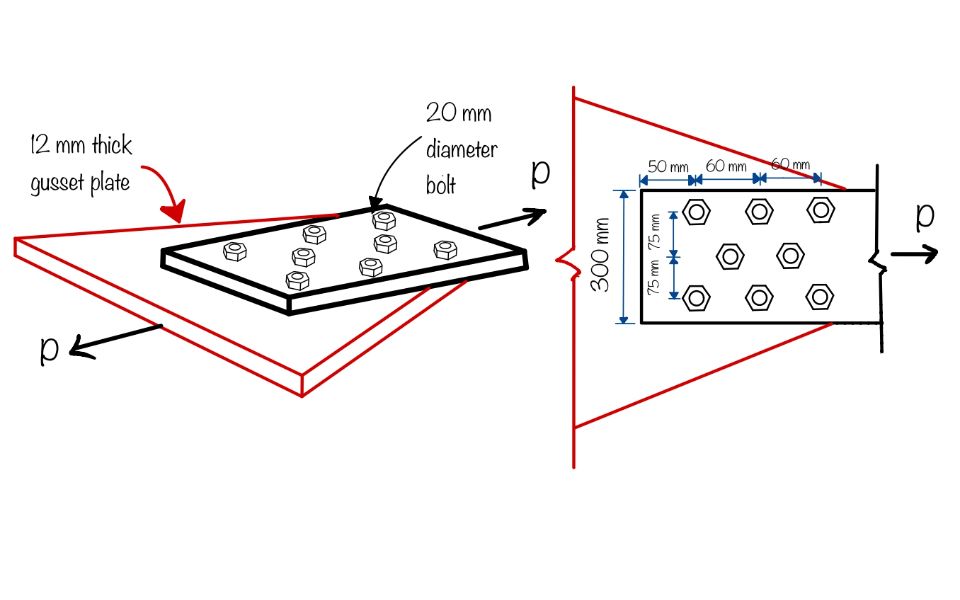
How to calculate design strength due to yielding of the gross section $(T_{dg})$
As per IS 800:2007, the design strength of member governed by $T_{dg}$ is given as:
$$ T_{dg}=A_gf_y/\gamma_{m0} $$
where,
$f_y=$ yield stress of the material
$A_g=$ gross area of cross-section
$\gamma_{m0}=$ partial safety factor for failure in tension by yielding (Table 5, IS 800:2007)
In the current design example, for 300 ISF 8 mm we have,
Width of the plate, $b=300\; mm$
Thickness of the plate, $t=8 \; mm$
Hence, $A_g=b\times t = 300 \times 8 = 2400 \; mm^2$
Therefore,
$$ T_{dg}=A_gf_y/\gamma_{m0}=2400\times 250/1.1 = 545.45 \; kN $$
How to calculate design strength due to rupture of the critical section $(T_{dn})$
As per IS 800:2007, the design strength of member as governed by $T_{dn}$ is given as:
$$ T_{dn}=0.9A_nf_u/\gamma_{m1} $$
where,
$f_y=$ Ultimate stress of the material
$A_g=$Net effective area of cross-section
$\gamma_{m0}=$ partial safety factor for failure at ultimate stress (Table 5, IS 800:2007)
How to calculate the net section area, $A_n$ for staggered bolting pattern?
As discussed in the article, the net effective area, $A_n$ of a cross-section is basically the expected path of rupture of the plate when subjected to tensile load. Thus, it will fail through the bolt-hole path (staggered or linear) for the lowest effective net cross-section area.
IS 800 :2007 defines net section area for flat plates as:
$$ A_n=[b-nd_h+\Sigma\frac{p_{si}^2}{4g_i}]t $$
where,
$b, t=$ width and thickness of the plate respectively,
$d_h=$ diameter of the bolt hole
$g=$ gauge length between bolt holes (centre-to-centre distance of the bolt measured perpendicular to the direction of applied load)
$p_s=$ staggered pitch length between bolt holes, as shown in figure below.
$n=$ number of bolt holes in the critical section
$i=$ subscript for summation of all the inclined legs
Steps to select the path for calculating $A_n$
The focus is to calculate the minimum effective net area through which rupture of flat plate is possible. In such as case, follow the steps:
1) Select from a corner (extreme left or right depending on the pattern of bolting)
2) Select the suitable bolt lines through which failure can happen. For this, the thumb rule is:
a) Failure lines cannot propagate $90^\circ$.
b) Draw the lines in slant or downward fashion.
In the given problem, the following failure lines are possible.
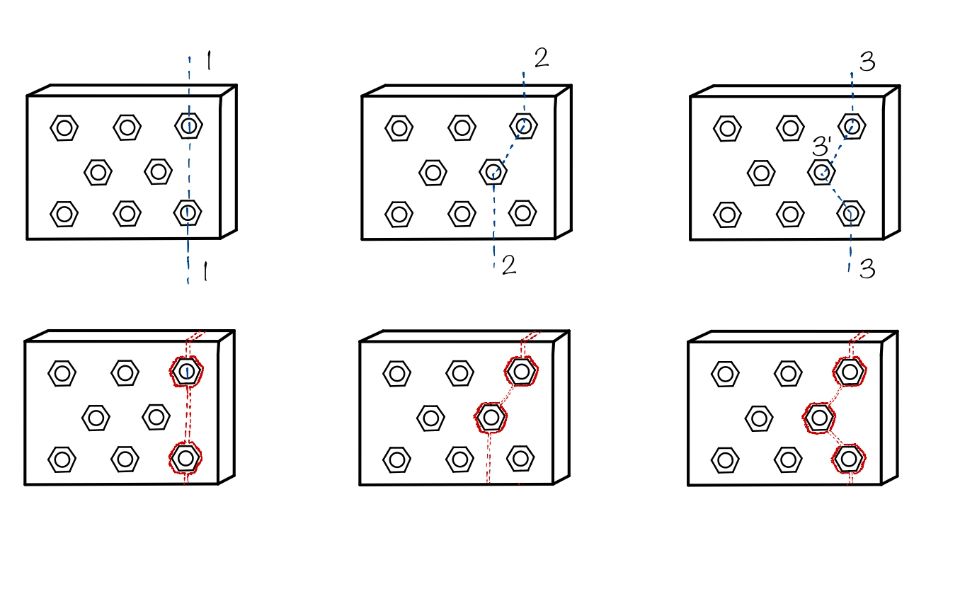
3) Calculate the net effective area $A_n$ as per Clause 6.3.1 IS 800 :2007
For the given problem,
Line 1-2-3
$b=300\; mm$
$n=2$
$n’=0$ $d_h=22\; mm$ i.e. $20+2=22\; mm$ as per Clause 6.3.1 IS 800 :2007
$t=8\; mm$
Hence, $A_n=[b-nd_h]t=[300-2\times22]\times8=2048\; mm^2$
Line 1-4-5
$b=300\; mm$
$n=2$
$n’=1$ $d_h=22\; mm$ i.e. $20+2=22\; mm$ as per Clause 6.3.1 IS 800 :2007
$p_s=60\; mm$
$g=75\; mm$
$t=8\; mm$
Hence$,$
$$ A_n=[b-nd_h+\Sigma\frac{p_{si}^2}{4g_i}]t $$
$$ A_n=[300-2\times 22+\frac{60^2}{4\times 75}]\times 8=2144 \; mm^2 $$
Line 1-4-2-3
$b=300\; mm$
$n=3$
$n’=1$ $d_h=22\; mm$ i.e. $20+2=22\; mm$ as per Clause 6.3.1 IS 800 : 2007
$p_s=60\; mm$
$g=75\; mm$
$t=8\; mm$
Hence$,$
$$ A_n=[b-nd_h+\Sigma\frac{p_{si}^2}{4g_i}]t $$
$$ A_n=[300-3\times 22+2\times\frac{60^2}{ 4\times 75}]\times 8=2064 \; mm^2 $$
Line 1-4-6-7
$b=300\; mm$
$n=3$
$n’=1$ $d_h=22\; mm$ i.e. $20+2=22\; mm$ as per Clause 6.3.1 IS 800 : 2007
$p_s=60\; mm$
$g=75\; mm$
$t=8\; mm$
Hence$,$
$$ A_n=[b-nd_h+\Sigma\frac{p_{si}^2}{4g_i}]t $$
$$ A_n=[300-3\times 22+2\times\frac{60^2}{ 4\times 75}]\times 8=2064 \; mm^2 $$
Thus, for the given problem failure will happen in bolt line 1-2-3
Hence, $A_n=2048\; mm^2$
Now, $T_{dn}=0.9A_nf_u/\gamma_{m1}=0.9\times 2048\times 410/1.25=604.6\; kN$
How to calculate design strength due to block shear $(T_{db})$
As per IS 800: 2007, the design strength of member ruled by $T_{dg}$ is given as:
$$ T_{db}=Min(T_{db_1},T_{db_2}) $$
Now for different cases
$$ T_{db_1}=\frac{A_{vg}f_y}{\sqrt{3}\gamma_{m0}}+\frac{0.9A_{tn}f_u}{\gamma_{m1}} $$
Now considering the different case
$$ T_{db_2}=\frac{0.9A_{vn}f_u}{\sqrt{3}\gamma_{m1}}+\frac{A_{tg}f_y}{\gamma_{m0}} $$
where,
$f_y=$ yield stress of the material
$f_y=$ ultimate stress of the material
$A_{vg}, A_{vn}=$ minimum gross and net area in shear along bolt line parallel to external force respectively (refer to figure shown below)
$A_{tg}, A_{tn}=$ minimum gross and net area in tension from the bolt hole to the end bolt line (to the end in case of angle), normal to the line of force (refer to figure shown below)
For the given problem,
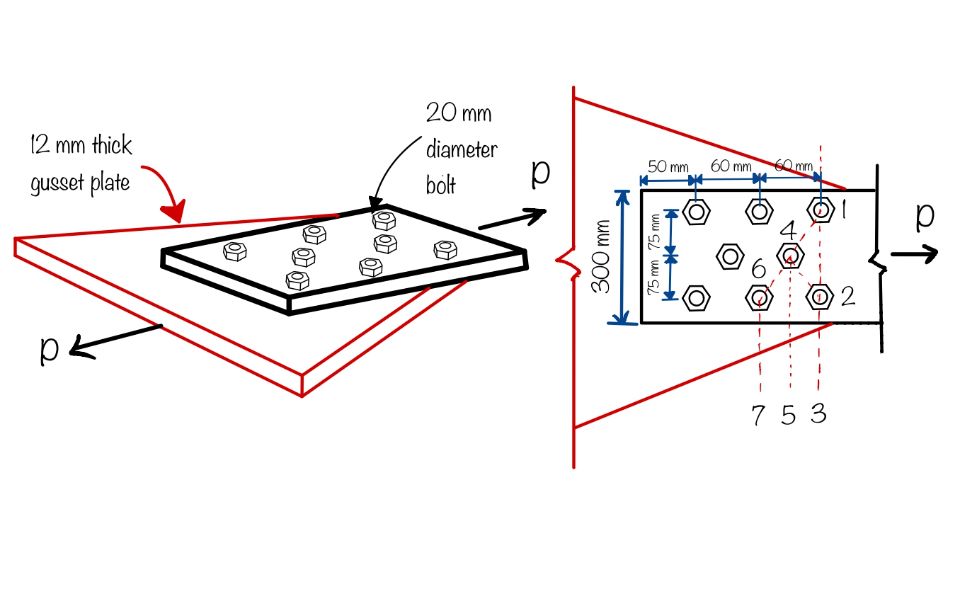
For calculation of gross shear area and gross tensile area refer to previous article.
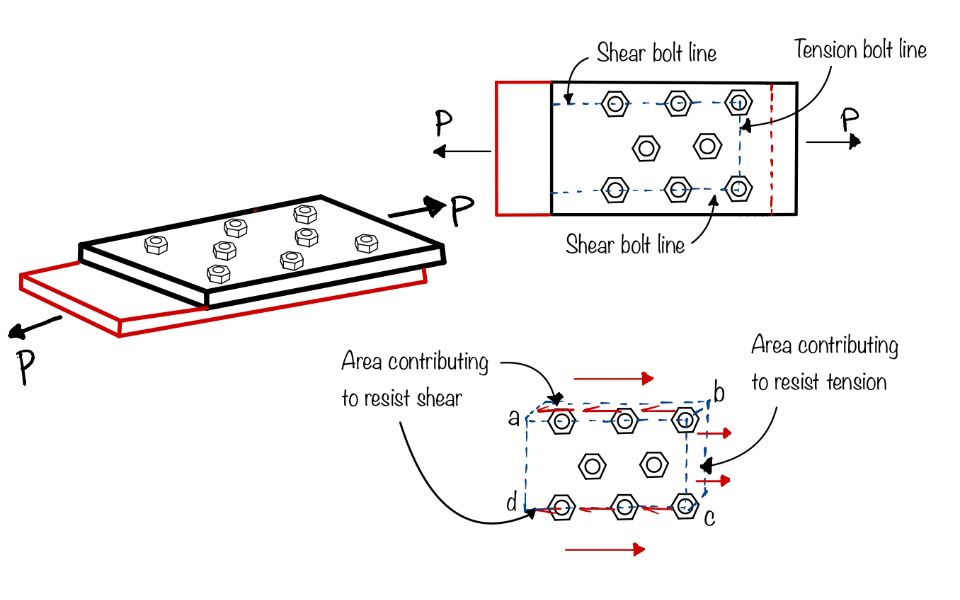
$A_{vg}=$ Gross area along $ab$ and $cd$ $=2\times[(50+60+60)\times8]=2720\; mm^2$
$A_{vn}=$ Net area along $ab$ and $cd$ $= 2\times[(50+60+60-2.5\times22)\times8]=1840\; mm^2$
$A_{tg}=$ Gross area along $bc$ $=(75+75)\times8=1200\; mm^2$
$A_{tn}=$ Net area along $bc$ $=(75+75-2\times22)\times8=848\; mm^2$
Therefore,
$$ T_{db_1}=\frac{A_{vg}f_y}{\sqrt{3}\gamma_{m0}}+\frac{0.9A_{tn}f_u}{\gamma_{m1}} $$
Similarly for second case
$$ T_{db_1}=\frac{2720\times250}{\sqrt{3}\times1.10}+\frac{0.9\times848\times410}{1.25}= 607.24 \; kN $$
again
$$ T_{db_2}=\frac{0.9A_{vn}f_u}{\sqrt{3}\gamma_{m1}}+\frac{A_{tg}f_y}{\gamma_{m0}} $$
$$ T_{db_2}=\frac{0.9\times1840\times410}{\sqrt{3}\times1.25}+\frac{1200\times250}{1.10}=586.33\; kN $$
Hence, $T_{db}=586.33\; kN$
Thus, design tensile strength, $T_d=\text{Min} (T_{dg},\,T_{dn},\,T_{db})= T_{dg}=545.45 \; kN$
Conclusions
In this article, we have seen how to calculate the tensile strength of a flat plate with staggered bolting pattern with a design example. Hence we can compare both types of bolting.
In this article you have learned the following key points:
- Net section: Determination of net section area, $A_n$ is an important step in design strength calculation.
- Staggered bolting: Staggered bolting minimizes the reduction in net effective area.
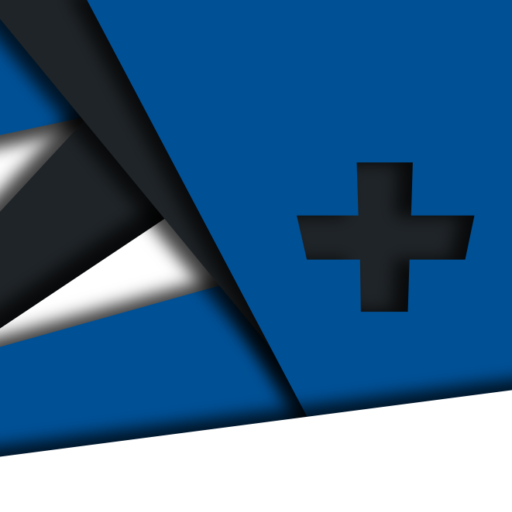
Android Apps
⭐️ ⭐️ ⭐️ ⭐️ ⭐️ 1000+ | 400,000 + Downloads (Cumulative)
At eigenplus, our goal is to teach civil engineering students about structural analysis and design starting from the fundamental principles. We do this with the help of interactive android applications and accompanying web articles and videos.
Our apps have helped more than 400 thousand students across the world to understand and learn the concepts of structural engineering. Check out our apps on the google play store.
This article was crafted by a group of experts at eigenplus to ensure it adheres to our strict quality standards. The individuals who contributed to this article are:
Author
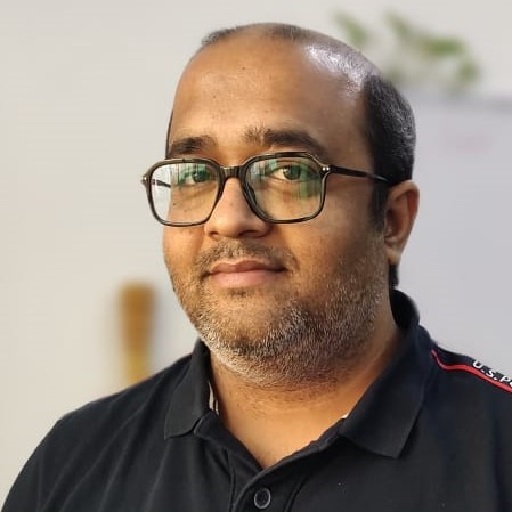